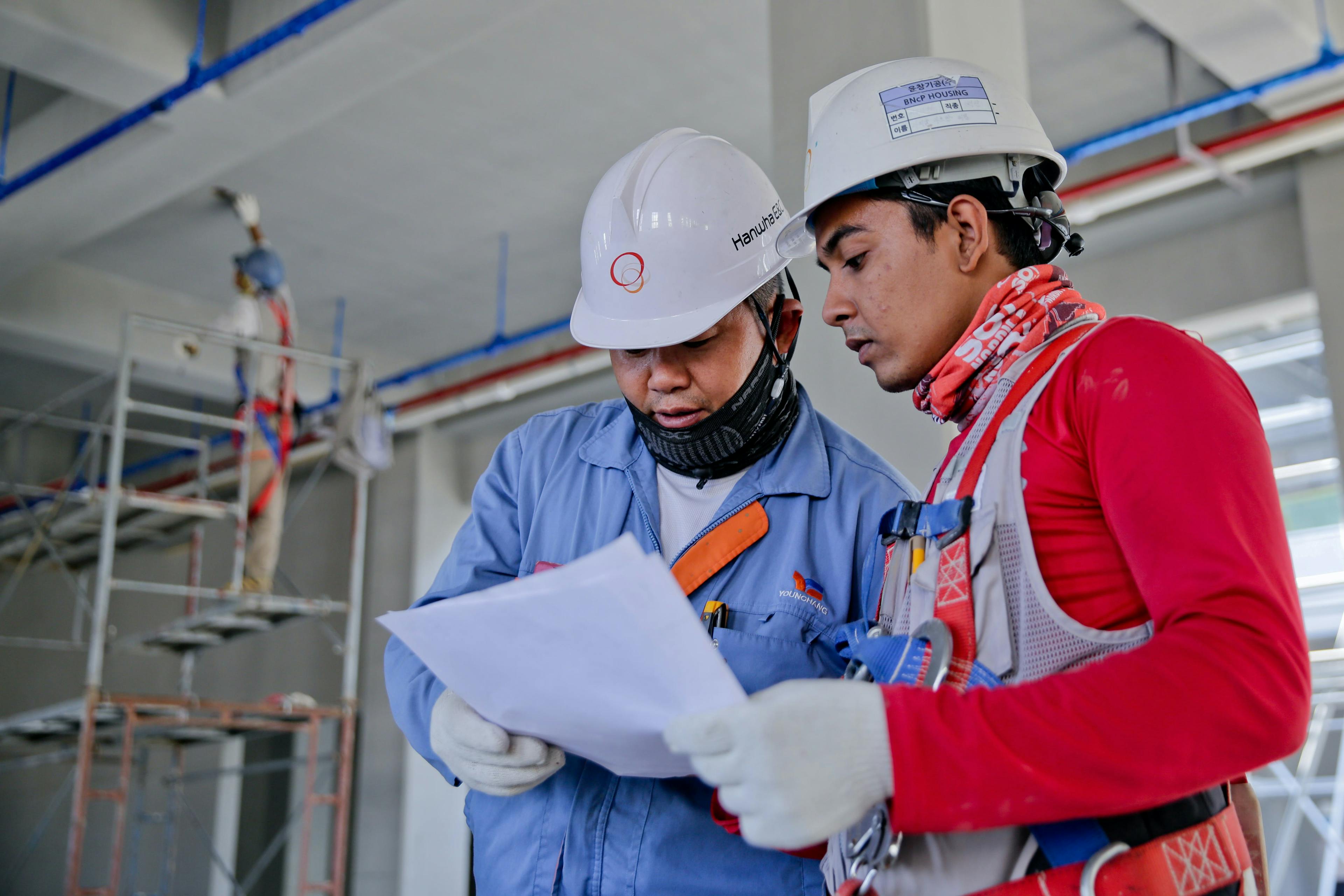
Integrate energy management systems in pulp and paper mills
Summary
Integrating the ISO 50001 Energy Management System leads to significant GHG emissions reductions and cost savings.
Context
CMPC, a multinational firm, produces fiber-based goods like wood, pulp, and various paper products. It operates sustainable, certified plantations and focuses on recyclability. The company is structured into three main units and a subsidiary:
Celulosa handles forestry, nurseries, and wood and pulp sales, with facilities in Argentina, Brazil, and Chile.
Biopackaging offers virgin and recycled fiber packaging solutions, operating in Argentina, Chile, Mexico, and Peru.
Softys, the subsidiary, produces tissue and personal care items from cellulosic fibers, with operations across eight countries in South America.
CMPC's energy consumption per business area is illustrated in Figure 1 below.
Figure 1: CMPC's energy consumption by business areas

Demonstrated in Figure 2 below, biomass is CMPC's main energy source, followed by natural gas, electricity, fuel oil, coal, and others..
Figure 2: CMPC's energy consumption by fuel source

CMPC is a company with high energy consumption in its production processes (lime kilns, recovery boilers, power boilers, paper machines, thermal plants, etc.), amounting to approximately 37,036 GWh per year, with 81% primarily sourced from renewable energy. Therefore, the 19% derived from fossil fuel energy emits GHGs and can be reduced through management measures, operational efficiency, or technological upgrades.
CMPC has committed to achieving Net Zero by 2040 and has SBTi-validated targets to reduce absolute Scope 1 and 2 GHG emissions by 50.4% by 2030 (2018 base year) and Scope 3 GHG emissions by 37.5% by 2035 (2020 base year).
Solution
Implementing Energy Management Systems
Since 2014, CMPC has prioritized and implemented Energy Management Systems (EnMS) as a decarbonization lever, resulting in significant reduction in GHG emissions and cost savings. These EnMS have been implemented at 26 production plants, which is equivalent to 96% of the energy consumption of all CMPC industrial plants in eight Latin America countries and 37,036 GWh/year (2022).
To implement EnMS, CMPC followed each of the ISO 50001:2018 Pillars:
Develop a policy for more efficient use of energy: Celulosa, in its energy policy, declares its commitment to produce, process, and market pulp, wood, and paper in a sustainable manner, permanently seeking to balance the development of its businesses with optimal energy performance requirements, and improving its energy performance constantly.
Fix targets and objectives to meet the policy: CMPC annually establishes its management objectives and goals in a manner that is compatible with its other objectives, ensuring the availability of resources and related data to achieve them.
Use data to better understand and make decisions about energy use: CMPC manages energy data scientifically, ensuring the correlation between energy production and consumption to project performance and establish goals.
Measure the results: CMPC measures results and compares them with initial projections to ensure benefits are captured.
Review how well the policy works: CMPC reviews energy policy and ensures that resources are available to meet goals.
Continually improve energy management: To assure continuous improvement, CMPC uses the SDCA cycle (Standard, Do, Check, Act), to determine the process variables that significantly impact energy performance.
In addition to the ISO pillars, CMPC implemented the following strategies to improve energy efficiency across their industrial plants:
Inspire plant-driven ideas for energy performance improvements, allowing implementation without competition from projects of different natures or regulatory commitments. This approach has been embraced across various plants.
Ensure best practices transferred to every plant when the respective corporate area managing EnMS are working on multiple sites. This maximizes the benefits obtained from replicable projects.
Integrating energy management into operational excellence
To improve energy performance, CMPC has also integrated energy management into operational excellence. One of the ways the company has approached the relationship between operational and energy performance is through management indicators. The main indicator for operational management is Overall Equipment Effectiveness (OEE), which breaks down into the following:
OEE=availability x performance x quality
This indicator allows CMPC to assess how much of a productive advantage is achieved at a particular organization, process, or asset – in other words, how efficient it is in terms of its purpose. This strategic measure improves productivity by making energy efficiency another component of process optimization. Joining operational excellence and energy performance has enabled a faster understanding of how operational areas impact energy management, assigning responsibilities and adding energy to the list of work duties. In this manner, they avoid duplicity in administrative workloads at a rate of approximately 40% of all tasks associated with ISO 50001:2018. Ultimately, energy performance improves thanks to operational control, asset management, and improvement projects. As mentioned earlier, each facility with an EnMS plan was oriented toward the goal of improving energy performance by 5% in the first year, which was fulfilled by 100% of the 26 EnMS facilities. After this, goals are established in accordance with energy revisions and planned improvement projects. These objectives are monitored on a monthly basis in management meetings, which promote maintaining updated energy action plans where projected energy consumption is compared using the baseline with real consumption. The goal is to cover savings generated by improvement projects and the current state of progress.
Impact
Climate Impact
Targeted emissions sources
Scope 1 and 2
Decarbonization impact
With the implementation of the EnMS in 2014, the reduction in GHG emissions – based on the market-based method for Scope 2 – amounted to 250,916 tCO2e by the end of 2022, contributing to the corporate target of absolute reduction of Scope 1 and 2 GHG emissions, as demonstrated in Table 1 below. The reduction is established considering the base year of implementation for each industrial plant until the end of 2022.
Table 1: Impact from EnMS at CMPC
Industry | Pulp and Paper |
Product/Service | Pulp, boxboard, wood, packaging, tissue paper, and personal care products. |
Location | 26 sites in five countries |
Energy management system | ISO 50001:2018 |
Energy performance improvement period, in years | Total number of years for which energy was improved |
Energy Performance Improvement (%) over improvement period | Pulp Chile (three facilities): 27%; eight years (2014-2022) Pulp Brazil (one facility): 12%; two years (2022) Wood (six facilities): 7.5%, two years, 2022 Biopackaging (four facilities): 3.4%, two years, 2022 Softys Latam (eight facilities): 19.3%, in 2022 |
Total energy cost savings over improvement period | USD 112.38M |
Total Energy Savings over improvement period | 13,232 MWh |
Total GHG emissions reduction over improvement period. Market-based method | 250,916 tCO2e |
Business impact
Benefits
As demonstrated in Table 2 below, CMPC has recorded significant energy savings and cost savings of over USD 112M by implementing EnMS, certified with ISO 5001, in its business areas. To date, the company has observed that half of energy savings were accumulated from process optimizations and operational performance, both of which typically don’t require large investments.
Table 2: Energy, financial, and environmental benefits accrued through EnMS by CMPC's business areas (year 2022)
Business | Period | Energy Savings [MWhe] | Costs Savings [MUSD] |
---|---|---|---|
Celulosa | 2014-2022 | 13,009 | 107.2 |
Biopackaging | 2019-2022 | 115 | 3.0 |
Softys | 2015-2022 | 108 | 2.4 |
Total | 2014-2022 | 13,232 | 112.7 |
Costs
Globally, CMPC invested approximately USD 23.8M in measurement improvements, technological upgrades, and consultancy.
Implementation
Typical business profile
ISO 50001 is a versatile standard that applies to industries of any size and sector, contributing significantly to the reduction of costs and GHG emissions. Operational excellence is inherently a crucial driver for energy efficiency, making the establishment of a correlation between the two essential for any industry. Once maximum operational efficiency is achieved, it becomes even more important to invest in energy efficiency projects, such as technological upgrades or more efficient equipment, to further enhance performance and sustainability.
Approach
The strategic plan for energy management at CMPC has been in effect for six years, a plan that considers and includes the following timeline and stages:
1. Learning
The objective driving this phase was to achieve ISO 50001 certification for all three pulp plants in Chile, which account for 55% of energy consumption. The results were very encouraging (over 20% improvement in energy performance over three years) and the initiative was expanded to every plant in all three business units, independent of size, production, and energy consumption. Additionally, CMPC implemented the first waves of the pillars of Operational Excellence at Celulosa plants.
2. Expansion
In this stage, the goal was to achieve ISO 50001 certification in at least one plant in each business unit. This was first materialized in Softys Uruguay (in 2016) and in Biopackaging – Sack Kraft Chile (in 2018). This led to the inevitable conclusion that the benefits of implementing EnMS under ISO 50001 were significant, independent of the size of the facilities or business unit. This laid the foundation for a more aggressive implementation of the plan in the next phase as an integral part of the company’s corporate policy.
3. Consolidation
This stage consisted of consolidating energy management as a corporate policy for the organization. The goal was to certify at least 90% of all energy consumption for CMPC in 2020 under ISO 50001:2018. This meant certifying the EnMS for 19 plants over the course of a two-year period and updating to the 2018 version of ISO 50001 for all the plants that had been certified under the 2011 issuance of the standard. The company has achieved and surpassed this goal, certifying 26 plant and having 96% of their energy consumption managed by the ISO 50001: 2018 standard. Additionally, implementation of operational excellence was also expanded to other CMPC Biopackaging and Softys plants.
4. Integration
As a byproduct of the maturity of EnMS, great potential for integration was detected between the organization’s operational excellence model and EnMS. As such, this particular phase is centered on analyzing and structuring the integration process between both management models at CMPC Celulosa.
To that end, the Corporate Energy Efficiency team led the previously described integration process. The team also has a leader placed in each of the plants who is responsible for energy management at the facility and reliant on varying operational and transversal areas. These individuals act as change agents backed by top-tier management.
An important part of success is due to the transfer of knowledge from the lessons learned. These lessons are perennially transmitted onward to the teams and leaders at each facility, ensuring permanent evolution toward continuous improvement.
The plan also considered support from advising consultancies to train personnel, develop plans, establish energy performance indicators, develop energy revisions, and balance and launch improvement projects.
Stakeholders involved
To implement EnMS, CMPC has put together multidisciplinary management teams from the areas of processes, maintenance, production, and operational excellence, among others:
The Corporate Energy Efficiency team: Coordinates activities with the plant energy team and cross-sectional areas, such as the departments of communication, acquisitions, engineering, legal, risk, and human resources. The elements related to context, risk analysis, identification, and assessment of legal requirements are all executed in coordination with cross-section areas and the Corporate Energy Efficiency team, in conjunction with energy management teams.
Energy Management teams: Have a highly trained leader on-site at the plant, who represents a key area for energy consumption to bridge the gap between EnMS and processes. Additionally, the Energy Management team is trained in ISO 50001, energy audits, and internal audits and to date, the company has trained over 40 collaborators as leading or internal auditors in ISO 50001 IRCA.
External third parties: Process audits are exhaustive and implemented by independent third parties via international accreditation agencies.
External consultants and authorities: Consultants and authorities like Chile’s Ministry of Energy were also involved in the implementation of this solution.
Implementation and operations tips
From the eight years of experience in energy management with certified EnMS, CMPC recommends companies taking their first steps in energy management to implement these key success factors:
Corporate leadership: Ensure long-term commitments and allocate resources that match energy management ambitions.
Knowledge transfer: Ensure specialized transfer of knowledge and best practices across facilities to minimize risks and enhance efficiency.
Reliability: Support sites early on their energy efficiency journeys, offering a layer of trust within the organization.
Communication and commitments: Establish clear, assessable communication and commitments at each facility.
Methodology integration: Integrate existing methods and structures for swift adoption of the energy management model.
Strategic alignment: Align energy goals and indicators with the company's strategic objectives.
Investment in technology: Prioritize expenditure on measuring instruments, specialized consulting, and expert service providers to influence significant energy use.