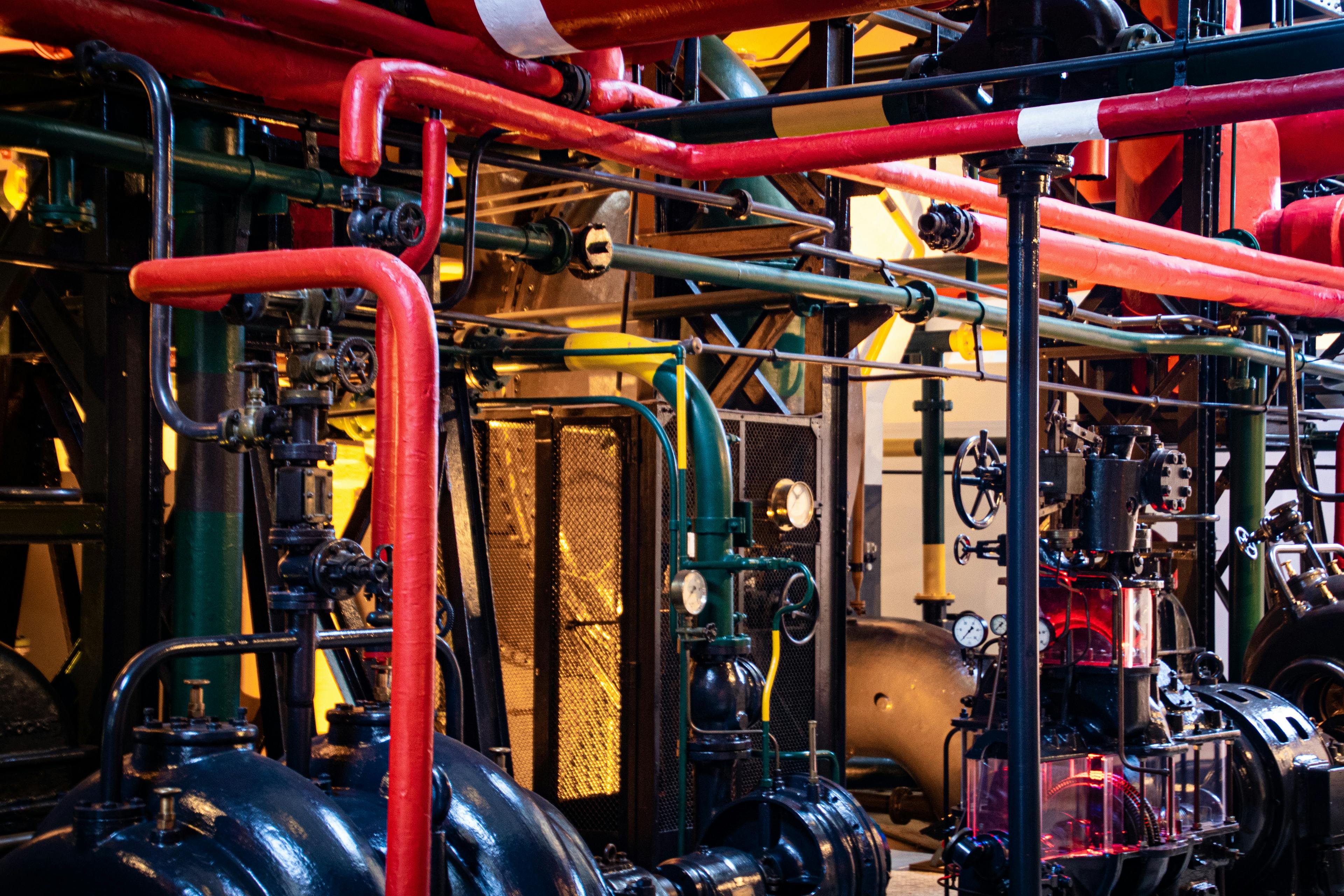
Reduce fuel oil through hydrogen substitution
Summary
By retrofitting an oil-fired lime kiln, the Pacífico pulp mill aims to reduce fuel oil consumption and GHG emissions by using residual hydrogen from a nearby sodium chlorate plant.
Context
CMPC is a global company that manufactures and markets fiber-derived products from its sustainable and certified plantations, as well as recyclable materials.
Pacífico mill is one of CMPC's four pulp mills situated near Angol in central-southern Chile, producing 530,000 tons of Bleached Softwood Kraft Pulp (BSKP) annually. The plant is adjacent to ERCO Company, the mill’s sodium chlorate supplier.
Sodium chlorate, used for pulp bleaching, is a crucial chemical input for the pulp production process and generates hydrogen as a byproduct. This byproduct used to be released directly into the atmosphere without any utility, buta project was planned and executed from 2007-2010 to substitute a portion of the fuel oil consumption in the lime kiln with the available and residual hydrogen, aiming to reduce GHG emissions, valorize the available hydrogen, and exploit this advantage in terms of cost efficiency, as economic savings were projected by replacing and reducing fuel oil consumption while harnessing a byproduct that was previously vented into the atmosphere (H2).
Solution
The project involved the retrofitting of the lime kiln, requiring the installation of a hydrogen purification and pressurization unit, both located at the supplier's facilities. It also entailed the establishment of a pipeline connecting the sodium chlorate plant to the lime kiln, the installation of a multipurpose oil burner capable of burning hydrogen along with fuel oil and other fuels (e.g., methanol), and the implementation of a process control system.
Figure 1: Process overview

In 2010 and 2011, the project made use of 30% of the available residual hydrogen for combustion, and gradually increased this proportion over time. By early 2012, this figure reached 60%, resulting in an undesirable effect on the evaporator plant and consequently leading to the suspension of the project.
Following extensive research and testing over the next year, the project team determined that due to the higher calorific value of hydrogen compared to fuel oil, there was degradation of the refractory bricks in the lime kiln. This material mixed with the liquors in the cellulose manufacturing process and subsequently, as part of the liquors cycle, precipitated as aluminum silicate, causing blockages and obstructions in the evaporators. The obstruction of the evaporators was resolved through evaporator washing procedures carried out during a general plant shutdown, which extended for an additional seven unplanned days.
As this project involves the conversion of a lime kiln originally designed for fuel oil consumption, its design and technical considerations were oriented toward that type of fuel. Part of the research resulted in preventive and control measures to ensure operational continuity. After numerous empirical tests and trials conducted by the plant itself, along with the technical constraints inherent to the lime kiln, including its design, geometry, and construction material, the target hydrogen burn rate will be 20%, expected to be achieved by the year 2024.
Following the implementation of these measures, the project resumed in 2021, demonstrating success to date, with a residual hydrogen burn rate ranging between 27% and 30%, equivalent to 5-6% of the total fuel of the lime kiln.
For the remaining vented residual hydrogen, another project is under development to use it in one of the steam boilers at the Pacífico mill.
Impact
Climate impact
Targeted emissions sources
The lime kiln is one of the major fixed sources of fuel oil consumption, serving as the primary energy consumer and, consequently, one of the largest GHG emission sources under Scope 1 in the plant's inventory.
The lime kiln is a crucial component in the kraft pulp production process, as it produces lime for white liquor production, which is a cooking chemical in the digesters, facilitating the separation of cellulose from lignin.
Although the project started in 2010, the measurement of GHG emissions impact considers 2018 as the baseline year due to: project suspension and resumption in 2021 due to a contingency, and the baseline year set in the target of reducing 50.4% of Scope 1 and 2 GHG emissions by 2030, established by CMPC and validated by the Science Based Targets initiative (SBTi).
In 2018, the total fuel oil consumption at the Pacifico plant represented 93%, with fuel oil being the main source of energy consumed by the lime kiln (98%).
Decarbonization impact
CMPC has a corporate goal of absolute reduction of scope 1 and 2 GHG emissions by 50.4% by 2030 from the base year 2018, validated by the SBTi.
With the implementation of the project, in 2022, the total fuel oil consumption at the Pacifico mill represented 74%, reducing the fuel oil consumption in the lime kiln from 98% to 90% (the remaining 10% was replaced by 5% hydrogen and 5% methanol). This fuel oil substitution resulted in a reduction of more than 15,500 tCO2e compared to 2018 emissions.
To achieve the goal of reducing 50.4% of absolute GHG emissions (Scopes 1 and 2) by 2030, CMPC has defined a roadmap of projects to be developed within its strategy. Of the total projects, 55% fall under the category of replacement and new technologies, 15% are dedicated to operational efficiency projects, 15% to innovation, 10% to electromobility projects, and 5% to management instruments for the acquisition of electricity generated by non-conventional renewable energy sources (NCRE). Regarding the decarbonization of Scope 3 GHG emissions, we expect to initiate a consultancy for the development of a roadmap in the fourth quarter of 2023.
Business impact
Benefits
Lower costs due to:
Substitution of fuel oil: $1.7M/year (at 2011 run-rate values).
Green tax payment: $77k/year . In Chile, there is a tax associated with CO2 emissions from stationary sources. By replacing fuel oil consumption with hydrogen, CO2 is no longer emitted into the atmosphere, and according to the mitigation orders of the emissions, this translates into a reduction of the green tax payment by approximately $77k/year .
Costs
Cost reduction: $1.8M/year. The reduction in the substitution of fuel oil costs by hydrogen was estimated after conducting a Free Cash Flow analysis, which took into account the savings from discontinuing the purchase of fuel oil, operational costs, and maintenance expenses.
Investment: $1.4M/total project (in USD year 2007). The project investments primarily included piping, valves, pumps, control system, a hydrogen washing system, and the purchase of a multipurpose burner to burn hydrogen and other fuels (fuel oil and methanol). The project was implemented in less than one year, with the burner delivery time being the longest delay.
Cost savings depend on the fuel oil price and the CO2 tax price.
Impact beyond climate and business
Co-benefits
Reduction in the number of trucks transporting fuel from the port to the Pacífico mill, leading to socio-environmental benefits such as decreased traffic congestion, fewer traffic accidents, reduced noise pollution, and a decrease in local pollution from particulate matter and other harmful gases.
Additionally, by consuming less fuel oil, there is a reduction in Scope 3 GHG emissions resulting from fuel imports.
Implementation
Typical business profile
Large fuel oil consumers (approximately 20,000 metric tons of fuel oil) with nearby hydrogen access (without the need to compress and transport hydrogen by truck. Ideally, with on-site production).
Pulp mills with integrated chemical plants that manufacture chlorine-soda derivatives and/or generate surplus hydrogen as a byproduct of the chemical process, or industrial plants within an industrial hub that coexist with hydrogen generation plants.
Approach
This project was developed with a cost-efficiency focus by using the hydrogen generated as a byproduct in the manufacturing of sodium chlorate by our supplier ERCO. This hydrogen could be harnessed as a fuel to replace a portion of the fuel oil consumption in the lime kiln, leading to a consequent reduction in Scope 1 GHG emissions and, eventually, Scope 3 emissions (particularly in fuel imports and transportation).
Below is a brief step-by-step overview of the project implementation:
Conceptual Study (determination of key quantities)
Go & See (similar experiences and recommendations)
Business Case
Environmental Assessment
Basic Engineering (Class 10 budget)
Go/No-go (economic evaluation, risk management)
Detailed Engineering
Procurement, Civil Works, Electromechanical Assembly, Commissioning
Operation and Ex-Post Evaluation
Stakeholders involved
CMPC, in collaboration with ERCO, its sodium chlorate supplier, executed this project. Additionally, the Pillard Company played a pivotal role as the supplier of the multipurpose burner, a critical component in the project due to its specific technical specifications for hydrogen combustion. Lastly, such projects required collaboration with local environmental authorities to obtain the necessary permits and conduct the required environmental assessments.
The investment was made 100% by CMPC.
Key parameters to consider
Hydrogen flame control: Due to its invisible nature and high calorific power, the hydrogen flame can affect the refractory walls of the lime kiln, introducing some of its components into the cellulose production process, which may have adverse effects. For instance, Pacífico mill experienced an event where aluminum silicate from the lime kiln refractories, carried by the lime produced, entered the white liquor. Through the cellulose production process and liquor cycle, it precipitated in the evaporator, resulting in reduced efficiency in the black liquor concentration capacity and affecting operational continuity.
This situation is primarily attributed to the retrofitting of the existing lime kiln.
Implementation and operations tips
Given the existing lime kiln requires retrofitting, there are technical reasons related to the lime kiln's design, geometry, and construction materials at Pacífico mill that limit the proportion of hydrogen to be burned to 20%. Each plant must assess the technical and economic feasibility of this approach.
It is suggested to consider the following:
Design parameters of the lime kiln.
Calorific value of hydrogen.
Control of variables: Visibility of the flame (hydrogen's invisible flame), chemical reactions of the processes, etc.
The main KPIs for hydrogen combustion control of the project are as follows:
Composition
Hydrogen: 91.29%
Oxygen: 3.46%
Carbon dioxide: 0.31%
Water: 3.4%
Nitrogen: 1.54%
Chlorine: 1-3 ppm.
LHV (lower heating value): 2,600 kcal/kg.
Supply Pressure Limit: 2.05 barg.
Supply Temperature Limit: 30-65 °C.
Burner Feed Flow (maximum): 5,233 Nm3/h.