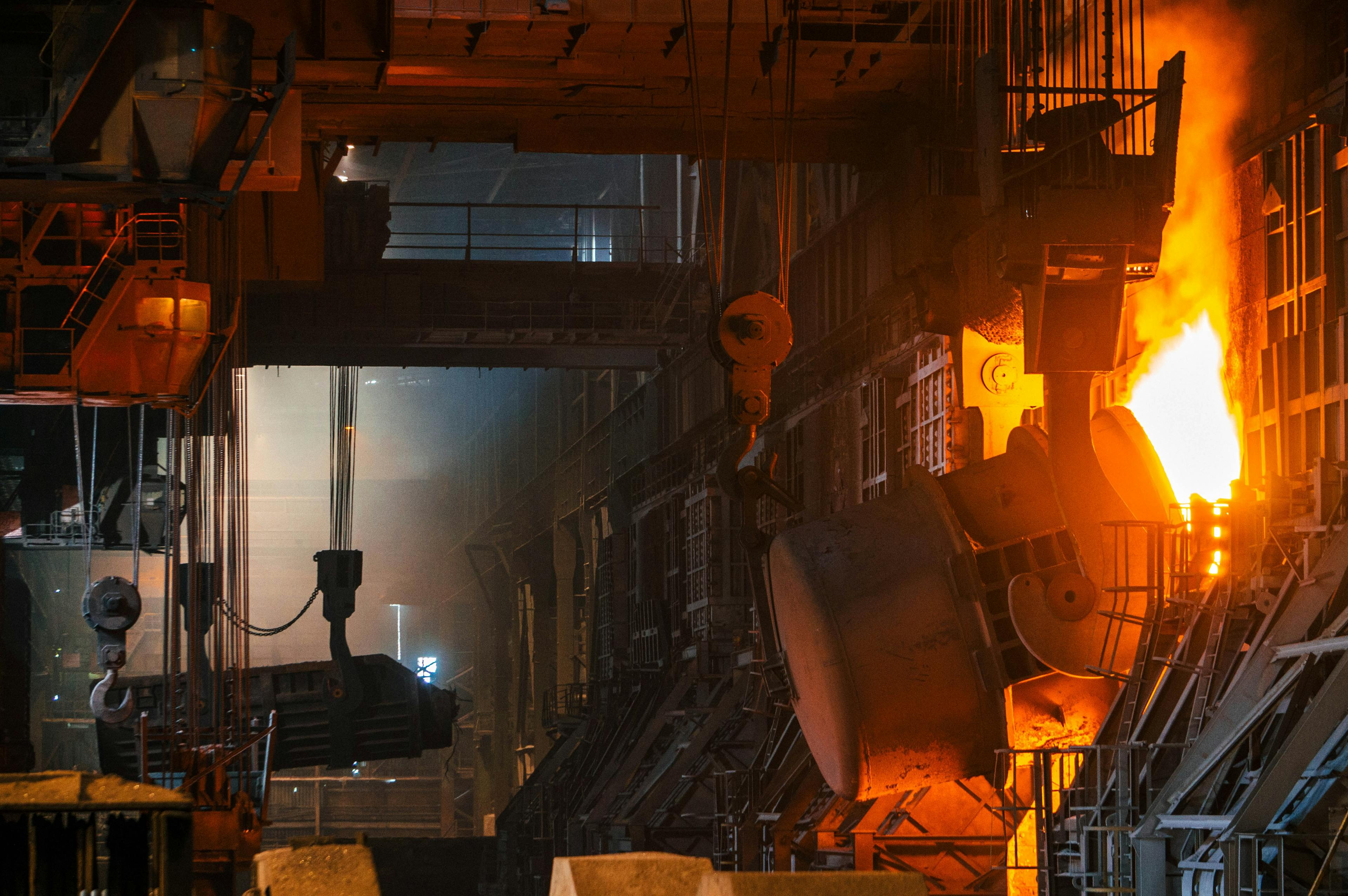
Switch to renewable energy to decarbonize industrial heat
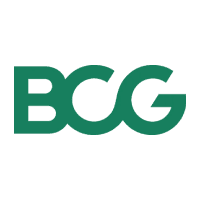
Summary
Low- or zero-carbon fuels and renewable energy technologies allow heat-intensive industries to reduce emissions from combustion of fuels (e.g., in manufacturing facilities)
Context
Industrial emissions represent 24% of total global emissions (1). Whereas high-temperature applications (>500⁰C) in hard-to-abate sectors represent a relatively small percent of total emissions, low (<130⁰C) and medium-temperature (130-500⁰C) processes dominate industrial thermal emissions (they account for ~78% of total thermal emissions in the US) (2). These applications can be relatively feasibly served by renewable heating technologies in the near- to medium- term, with cost-effective solutions available in many instances for heating under <200⁰C.
Figure 1: Low & medium heat processes dominate industrial thermal emissions and account for ~78% of total industrial thermal emissions

Source: BCG, The Renewable Thermal Vision. Finding a Path Forward for Decarbonizing Thermal Energy in the US Industrial Sector
Solution
Industrial heat users can implement a variety of renewable thermal technologies in combination to effectively decarbonize emissions while meeting their temperature and heat needs. These solutions offer competitive levelized cost of heat (LCOH) profiles that are either already competitive with natural gas or are currently higher but expected to decrease.
Heat pumps:
Description: Heat pumps use electricity to transfer heat from natural surroundings (e.g., ground, air, water) or waste heat streams for process applications
Temperature profile served: Under ~130⁰C, which represents a large percentage of industrial thermal emissions (~43% in the US)
State of the technology: Total levelized cost of heat (LCOH) for heat pumps is cost competitive or even lower than natural gas today. Heat pumps are expected to be able to achieve a maximum temperature of ~200⁰C by 2030 and may become applicable for up to ~60% of industrial thermal energy consumption occurring under ~200⁰C (3)
Solar thermal:
Description: Solar thermal technologies capture radiant solar energy and directly convert it to heat, which can then be stored or used in industrial applications. There are two main types of solar thermal technology: non-concentrating and concentrating. Examples of non-concentrating systems are flat plate, evacuated tube integral collector storage, and thermosiphon collector. Examples of concentrating systems are parabolic trough, parabolic dish, and Linear Fresnel
Temperature profile served: Non-concentrating: up to 100⁰C; concentrating: theoretically up to 1,200⁰C.
State of the technology: Non-concentrating low temperature solar thermal is widely deployed for residential and commercial building water heating. Concentrating higher temperature industrial heating is at pilot and demonstrating phases in the US
Biomass:
Description: Biomass in this context is any organic matter that can be used as a source of heat suitable for high-temperature process applications through direct combustion, such as wood, crop residues, animal waste, and municipal solid waste. This solution has the potential to create significantly lower emissions than natural gas on a lifecycle basis, depending on the biomass and combustion process used
Temperature profile served: Temperatures up to ~1000⁰C
Current state of the technology: Biomass combustion is widely deployed in wood and pulp and paper industries for power generation and process heating applications
Electric resistance:
Description: Electric resistance (ohmic) thermal equipment uses an electric current to provide heating from a material's electrical resistivity
Temperature profile served: Up to 1,800⁰C
State of the technology: Electric resistance is a high maturity technology, as it is the simplest and oldest form of electric heating. However, it can have higher emissions relative to natural gas combustion, but if paired with renewable energy sourcing, can be carbon neutral. However, it may be expensive to implement
Renewable natural gas (RNG):
Description: RNG, also known as biogas or biomethane, is virtually identical in composition to fossil fuel-based natural gas used for industrial heat. RNG comes mainly from the processing of gases captured from landfills and wastewater treatment plants, and the anaerobic digestion of agricultural or food waste
Temperature profile served: Temperatures up to ~2000⁰C
Current state of the technology: RNG is produced in sizeable quantities across the US but supply still only constitutes <0.2% of total natural gas demand. RNG use is not expected to scale up further in the near term due to supply constraints, and only a fraction of demand is likely to be met by current and planned projects
Green hydrogen:
Description: Green hydrogen (i) is hydrogen that is produced with zero or near-zero emissions; for example, by electrolysis of water using clean electricity. Green hydrogen production has practically no CO2 emissions, and hydrogen combustion produces only water vapor and heat.
Temperature profile served: Temperatures up to ~2000⁰C
Current state of the technology: Hydrogen is supply-constrained in the near term and next generation technologies are nascent, resulting in an LCOH that is uncompetitive with natural gas. However, it has significant potential as a long-term sustainable fuel due to declining cost of hydrogen production and few feedstock constraints
Below (Figure 2) is a summary table of the temperature, maturity, and reasons for use of each technology. Market maturity is determined based on degree of technical development and market availability:
High: High level of technical development and market availability, with commercial maturity in the near term (1-2 years)
Medium: Technical development still in progress and/or market is still evolving, with potential for commercial maturity in the medium term (3-5 years)
Low: Low degree of technical development and likely will only be able to reach commercial maturity in the long term (5+ years)
Figure 2: Renewable technologies and characteristics

Source: BCG, Renewable technologies and characteristics
Usage
Usage
Heat-intensive industries are, for the most part, yet to adopt renewable heat alternatives, with some variation across industrial processes. In the paper industry, for example, 60% of total energy consumption comes from renewables (almost exclusively biomass). Cement relies on biomass for 18% of its energy consumption – the industry’s only renewable source of energy. The food industry’s total energy consumption uses 11% biomass and 1% solar energy. Other heat-intensive industries, like chemicals, iron and steel, and refineries, are unable to easily adopt renewables in their production processes and will need to replace their current energy sources (natural gas, coal, and petroleum) with renewable fuels (hydrogen, RNG), which are currently supply-constrained.
Impact
Climate impact
Targeted emissions sources
Renewable industrial thermal technologies facilitate emissions reductions, primarily in:
Scope 1 (of manufacturing companies): Reduction from avoided use of natural gas, petroleum, and coal, as well as potentially lower process emissions through electrification or hydrogen usage in relevant industries.
Scope 2 (of company purchasing electricity, heat, and steam): If a company electrifies a process with grid electricity, Scope 2 emissions will increase, unless it is coupled with renewable energy procurement. Purchased steam and heat are part of Scope 2.
Scope 3: (for manufacturing companies): the most important sub-categories affected would be:
Category 1 (Purchased goods and services)
Category 3 (Fuel- and energy-related activities not included in Scope 1 or Scope 2)
Category 10 (Processing of sold products)
Category 12 (End-of-life treatment of sold products)
Decarbonization impact
The decarbonization potential of renewable heat varies across industries, mainly depending on the temperature of heat needs and the deployable renewable thermal technologies.
From a technical standpoint, heat pumps can address most low-temperature needs and there are good alternatives for medium-grade heat. For example, in the US, a vast majority of industrial heat needs for food manufacturing are in the low temperature range, which can be decarbonized on an accelerated timeline with heat pumps, especially where electricity grids have (or plan to have) a high proportion of renewables.
For high-temperature processes, the solutions exist but are more expensive. For example, the chemicals and refining industries would require green hydrogen to replace natural gas for combustion, which is not readily available yet. Fully decarbonizing heat in these industries may require the use of renewable energy in combination with other fossil-based solutions, coupled with carbon capture and storage (CCS) for significant decarbonization impact. Deployment of decarbonized high-heat options will depend on continuing reduction in cost, increased marketability, and a skilled labor force.
If we assume that most of the low-temperature (<130°C) and medium-temperature (130-500°C) can be decarbonized, up to 78% of industrial thermal emissions can be addressed in the US (see Context). Similar proportions may be possible in other countries.
Business impact
Benefits
Reduced market risk: Reduced reliance on imported fossil fuels exposed to significant market volatility, and consequently potential reductions in price volatility and insulation from supply disruptions, if coupled with own renewable generation or a power purchase agreement (PPA)
Cost reductions over long term: Long-term cost-effectiveness, as renewable thermal solutions can offer cost advantages over conventional fossil fuels in the long run. Though the initial capital costs for transitioning to renewable technologies can be high, the LCOH for renewables is either already competitive with natural gas (e.g., heat pumps) or expected to decline (e.g., hydrogen). Fossil fuels are expected to become more expensive. Additionally, solutions like biomass can provide cost reductions due to avoided waste
Local/regional environmental and community benefits: Greater community acceptance and reduced regulatory scrutiny, as switching to renewable sources in industrial processes can improve air quality and reduce GHGs
Brand benefits: Enhanced brand reputation, as customers seeking sustainable products will look favorably at companies using renewable heat
Costs
Impact on operating costs: Given the higher LCOH for many thermal decarbonization technologies today, operating costs can be expected to increase, especially in the short run, as renewable energy supply remains constrained
Investment required: Capital investment will depend on industry heat requirements and existing infrastructure. The investment required should be assessed on a site-by-site basis
Subsidies used: Regional and country-specific subsidies apply (e.g., green hydrogen incentives from Inflation Reduction Act in the US)
Other dependencies: Cost mostly depends on local factors (e.g., solar availability, biomass feedstock availability, and green hydrogen infrastructure). Companies should also consider the time horizon of their planned capital upgrades. If a company needs to make large capital investments (e.g., plant upgrades, new plants) in the near term, it should opt for technologies that require low capital investments relative to operational savings (e.g., heat pumps, solar thermal). If a company is only looking to make capital investments in, say, five years or more, it should begin to consider putting high-temperature fuel alternatives (green hydrogen, RNG) in place, as a longer time horizon may make these solutions commercially viable.
Indicative abatement cost
Assuming renewable technologies displace natural gas, indicative abatement costs per ton of CO2 are approximately as follows (ii):
Heat pumps: ~$40
Electric resistance: ~$250
Solar thermal: ~$50
Renewable natural gas: ~$200
Green hydrogen: ~$200 (~$100 in the US with IRA)
Biomass: ~$50
Impact beyond climate and business
Co-benefits
Increased employee and community safety and comfort from improved air quality
Reduced pressure on local landfill use through the reduction and use of biomass waste (e.g., manure, food waste)
Implementation
Typical business profile
This action is relevant to most industries that use process heat, including refineries, chemical, iron and steel, food, paper, and cement.
Solutions for low-temperature heating are much more advanced in terms of commercial maturity, making implementation more viable in the near term for industries such as food. Companies will need to evaluate the site-specific economics of implementation, including the cost of equipment and facility reconfiguration, the availability of relatively inexpensive clean energy, access to financing arrangements, the availability/sustainability of bio waste, and other relevant factors. Additionally, low-temperature technologies can even apply to high-temperature industries if implemented to heat buildings like office spaces and manufacturing sites.
High-temperature heat solutions face supply constraints and are therefore not easily or inexpensively realized for industries like iron and steel, and refineries. Viable economics will depend on adequate fuel supply, government subsidies, and other relevant factors.
Approach
Assess usage: Understand heat and temperature needs to identify potential thermal decarbonization options.
Explore heat reduction: Evaluate options to reduce both heat and/or temperature (via process or product redesign) without disrupting production and product quality (i.e., prioritize temperature and heat reduction before looking to decarbonize).
Select solution: Chooserenewable thermal options that could meet your thermal needs. Align with current replacement cycles wherever possible to avoid unnecessary costs (i.e., avoid near-term solutions that will become stranded assets). Approaches to thermal decarbonization will vary widely across industries. Exemplary solution mixes in some illustrative industries would be:
Food: Explore heat pumps and solar thermal to displace natural gas and other fossil fuel combustion, which can likely be completed on an accelerated timeline
Iron and steel: Phase out blast furnaces/basic oxygen furnaces over time in favor of electric arc furnaces with green hydrogen (using direct reduced iron)
Paper: Use biomass combustion to address most thermal energy needs, making sure sustainable biomass is used. Fossil fuels can be displaced through increased use of waste biomass and supplemented by electrification, as needed
Identify vendors: Identify the (new or current) vendors or service providers who can support implementation of these renewable thermal technologies in the relevant geography. While this market is fast evolving, current types of service providers include energy services contractors, engineering firms, heating/cooling equipment manufacturers, building energy management providers, and in some cases, utilities.
Implement: Conduct retrofits (e.g., heat pumps, solar thermal) or install new renewable thermal equipment (e.g., biomass, boilers).
Stakeholders involved
An array of internal stakeholders must be involved to transition to renewable heat:
Executive Management: To decide on major capital expenditures and make long-term strategic and operational planning decisions to use renewable thermal energy
Strategy: To determine new business models resulting from changes in input costs and create sales strategies around decarbonized commodities (e.g., decarbonized steel)
Finance & Accounting: To assess budget availability and alignment for capital-intensive installation of new thermal solutions
Facility Managers: To manage facility retrofits accommodating renewable heating
Procurement: To implement a roadmap for sourcing new suppliers and negotiating contracts with renewables providers
Key parameters to consider
Solution maturity
Please see Solution section.
Technical constraints or pre-requisites
Capital investment capability and ability to partner with an energy provider to handle renewable energy capability, if energy expertise does not exist in-house.
Additional specificities
Regional clean grid availability and local regulation may generate further incentives/disincentives for renewable heat adoption.
Implementation and operations tips
Site considerations: Pursuing industrial thermal decarbonization without disrupting production and product quality will require a clear understanding of industrial site temperature needs and feasible technologies. Site-by-site determinations will need to be made regarding the forecasted changes in heat costs and the long-term business case for decarbonization.
Context considerations: Adoption should be pursued with an understanding of the local regulatory environment for incentives or disincentives. Additionally, the existing grid power generation from renewables and any expected system upgrades should be considered while determining the most impactful heat decarbonization technologies.
Adoption timing: Technology trends, government incentives, plant size, geographic availability of renewables, installation duration, and practical windows for upgrading (e.g., during extended facility maintenance) will affect adoption timing.
Market challenges: Market maturity and supply availability depend on the specific technology solution. For example, heat pumps and solar are highly mature technologies, whereas green hydrogen and RNG remain in nascent stages. In some cases, the local availability of cost-effective renewable heat might be years away.
Implementation partners: If energy expertise does not exist in-house, the company/supplier should identify the right energy partner with the capabilities necessary to help decarbonize industrial heat. This includes having the technical expertise, financial resources, and project management skills to successfully implement a decarbonization project.
Read more
The earlier discussion of renewable thermal technologies covered the description, temperature range, and state of the technology. Below are some other helpful details, such as decarbonization drivers, when to choose each solution, and other considerations.
Heat pumps
Primary driver of decarbonization: Heat pumps rely on high thermodynamic efficiency to drive decarbonization. They can achieve performance efficiencies of more than 300% (whereas natural gas is less than 85%) (4), because they move heat from where it is available to where it is needed, rather than generating heat. While grid power is used, and the current grid emissions profile would determine heat pumps’ effective emissions, grid power can and should become low carbon in many areas around the world. As such, heat pumps can eventually provide a (near) zero-carbon thermal source. Additionally, they can provide a near zero-carbon thermal source if coupled with company-owned renewable energy production or a PPA.
When to choose heat pumps:
Low grid electricity prices
Clean grid emissions profile or grids expected to become clean
Local alternatives (i.e., renewable fuels) are expensive
Upcoming facility upgrades, alongside which heat pumps can be installed
Suitable waste heat is available within the facility
Other factors to consider before implementation:
Facilities may need to be retrofitted to accommodate heat pumps (e.g., appropriate piping for thermal fluids)
Technology options, especially for higher heat, remain relatively limited
Energy service providers in many regions are still becoming familiar and trained to install and service this equipment
Solar thermal:
Primary driver of decarbonization: Zero emissions due to use of solar energy.
When to choose solar thermal:
Ample access to sunlight
Space availability for solar infrastructure
Low-temperature heat applications (with non-concentrating)
Timing of heat needed for operations is not critical, or have access to thermal storage
Biomass
Primary driver of decarbonization: Biomass is currently the most widely used renewable industrial heating source worldwide. However, biomass from waste feedstock has a higher emissions intensity profile than RNG and green hydrogen. It is not a long-term sustainable net-zero fuel, but it can play a role as a short-term bridge to Net Zero while RNG and clean hydrogen production and supply improve (5).
When to choose biomass:
On-site access to biomass supply or willingness to pay biomass transportation costs
Biomass being considered has a low emissions profile over full lifecycle
Other factors to consider before implementation:
Biomass requires high capital investment up front (e.g., to install biomass boiler and to process biomass waste onsite)
Electric resistance:
Primary driver of decarbonization: Electric resistance heating can directly replace most natural gas-fired industrial heating equipment without major system modifications. It can meet all industrial heating temperature requirements, aside from the highest temperature applications. Grid power is used; therefore, the current grid emissions profile would determine effective emissions.
When to choose electric resistance:
High-temperature heat is needed for industrial processes
Supplement needed for other sources to add temperature/heat
Other factors to consider before implementation:
Power infrastructure must be capable of handling higher loads; if insufficient, equipment upgrades can be capital intensive
Clean grid emissions profile or grid has plans to become carbon free
Electricity prices (including all price elements like demand charges, etc.)
Renewable natural gas (RNG):
Primary driver of decarbonization: RNG, once cleaned and processed, is fully interchangeable with conventional natural gas in terms of its heat profile. It has significant decarbonization potential, given that RNG production avoids methane emissions if feedstocks are left untreated (e.g., uncovered landfills), and it usually displaces use of extracted natural gas.
When to choose RNG:
High-temperature heat is necessary for industrial processes
RNG is available in sufficient quantity and at reasonable prices
Other factors to consider before implementation:
While landfill-derived RNG can be inexpensive, access is difficult due to lack of pipeline infrastructure around landfills
Green hydrogen:
Primary driver of decarbonization: Hydrogen is a combustible gas that can substitute natural gas in industrial high-temperature heating applications and has zero carbon emissions relative to natural gas during combustion. Emissions associated with hydrogen depend on how hydrogen is produced, and has practically zero emissions if produced by electrolysis using renewable electricity.
When to choose green hydrogen:
High-temperature heat is necessary for industrial processes
Willingness to pay price premium for decarbonization
Other factors to consider before implementation:
Technology is still being developed to ensure the effective transport and storage of hydrogen to avoid leakage and infrastructure deterioration (e.g., hydrogen transport via existing steel pipelines would not be possible due to steel embrittlement)
The safe transport and storage of hydrogen needs to be ensured, as it is highly combustible
Footnotes:
(i) Note: Other hydrogen production methods emit CO2 and are non-renewable (i.e., blue and grey H2). Black hydrogen is hydrogen produced from coal.
(ii) Note: Costs may depend on grid emissions profile. Methodology: marginal cost of renewable MMBTU is the delta between LCOH of renewable technology and natural gas, used EPA conversion for average carbon coefficient of pipeline natural gas burned carbon per MMBtu to find avoided CO2 per therm (6)