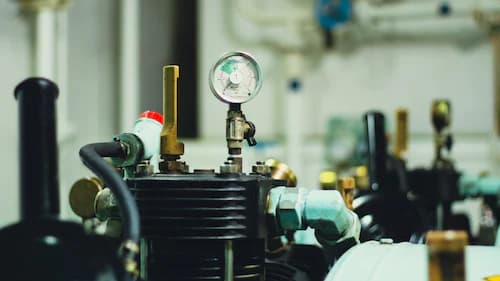
Use AI air compressor system to reduce energy consumption
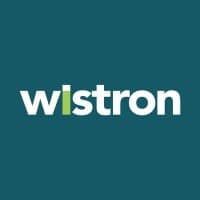
Summary
To minimize carbon emissions from facility equipment while ensuring production, an adaptive system of air compressors can reduce power consumption per finished good by 41%
Context
As orders increase year by year, manufacturing, power consumption, and the number of delivery trucks increase accordingly. The result has been an increase in carbon emissions. What's more, because daily power consumption often exceeds the maximum supply, production lines have had to shut down, causing extra production costs and wasted production capacity.
By deploying an AI air compressor control system in 2021, Wistron has achieved 41% carbon reduction in its factories across the world.
Solution
On-site pressure can change at any time, and production lines stop if pressure becomes too low. For Wistron, this meant being unable to control equipment efficiency and abnormalities automatically, relying only on manual start and stop of production lines.
The AI air compressor control system learns historical production plans and environment conditions (from a self-built weather station) on a bi-weekly rolling basis, and dynamically predicts and adapts to air pressure changes. A self-retrain mechanism is also deployed to ensure <5% error rate for the next one-hour forecast.
The best startup combination: Predicting air demand through machine learning and recommending the best startup combination based on environmental factors (measured by a self-built weather station) and production parameters
Smart group control of air compressors: The model can compensate gas supply according to on-site pressure value and fuzzy control, and automatically start and stop high-efficiency units and frequency conversion control
Self-learning: The AI model self-retrains regularly, and users continuously monitor whether the model data and model accuracy drift. They also compare estimated data with actual data in real time to ensure a <5% error rate, as well as capture and self-adjust seasonal transition information
Monitor consumption equipment: Wistron has installed power/water/gas meters to collect and monitor environmental parameters in real time, achieving precise control of the consumption of main equipment through electric baseline, electric prediction, and analysis of power, water, and gas
Impact
Climate impact
Targeted emissions sources
Scope 1: Reduced direct emissions from combustion of fuel (e.g., gas)
Scope 2: emission: Reduced indirect emission from electricity consumption
Decarbonization impact
Since 2021, by deploying the AI air compressor control system, Wistron has achieved 41% carbon reduction in its factories across the world.
Based on the company’s Climate Change Statement, which actively pursues decarbonization, Wistron is responding to the Paris Agreement and committing to limiting temperature increase to 1.5°C above pre-industrial levels. In December 2021, Wistron announced its goal to achieve carbon neutrality by 2030. Additionally, the company is committed to adopting the Science-based Targets initiative (SBTi) and will gradually implement net-zero actions.
Wistron is committed to reducing carbon emissions (Scope 1 & 2) by 4.2% per year, according to the SBTi methodology, and achieve carbon neutrality by 2030.
The company plans on increasing the proportion of renewable electricity is uses to 100% in 2030. In 2022, it achieved a significant milestone, with a renewable electricity usage rate of approximately 63%, reducing carbon emissions by 66.7% (Scope 1 & 2) compared to the baseline year.
Business impact
Benefits
Impact on operating costs: Power consumption reduced by 33% (Solar power, green electricity, and green electricity certificate)
Power consumption per finished goods: The electricity consumption of a single unit was reduced by 41%, which led to significant financial savings
Management efficiency: Generate real-time data and insights to improve management efficiency
Automation rate: Automatic data collection and parameter adjustment instead of manual work
Impact beyond climate and business
Co-benefits
Lower carbon dioxide emissions, increased air quality in industrial zones.
Potential side-effects
In the short term, the installation and maintenance of extra hardware devices (small weather station, PLC, sensor, etc.) may increase certain costs and power consumption, and increase carbon dioxide emissions.
Implementation
Typical business profile
This solution is fit for all kinds of factories using compressed air, as long as the air compressor supports IoT technology.
Approach
Identifying high energy consumption equipment
Modifying the equipment by installing sensors and controllers to monitor data and control the equipment
Integrating the data into the AI air compressor control system
Stakeholders involved
Project Leads: Manufacturing Director Company functions: Procurement and Facility Affair Department
Key parameters to consider
Solution maturity: Advanced – the solution has been implemented at multiple Wistron factories across the world
Technical constraints or pre-requisites: The air compressor needs to support IoT technology
Implementation and operations tips
At the beginning, the accuracy of the prediction model is not high, and prediction results may be erroneous, which will cause challenges. Large amounts of data is needed to feed the machine learning model to improve its prediction accuracy.