Switch to hybrid-electric furnace design in glass production
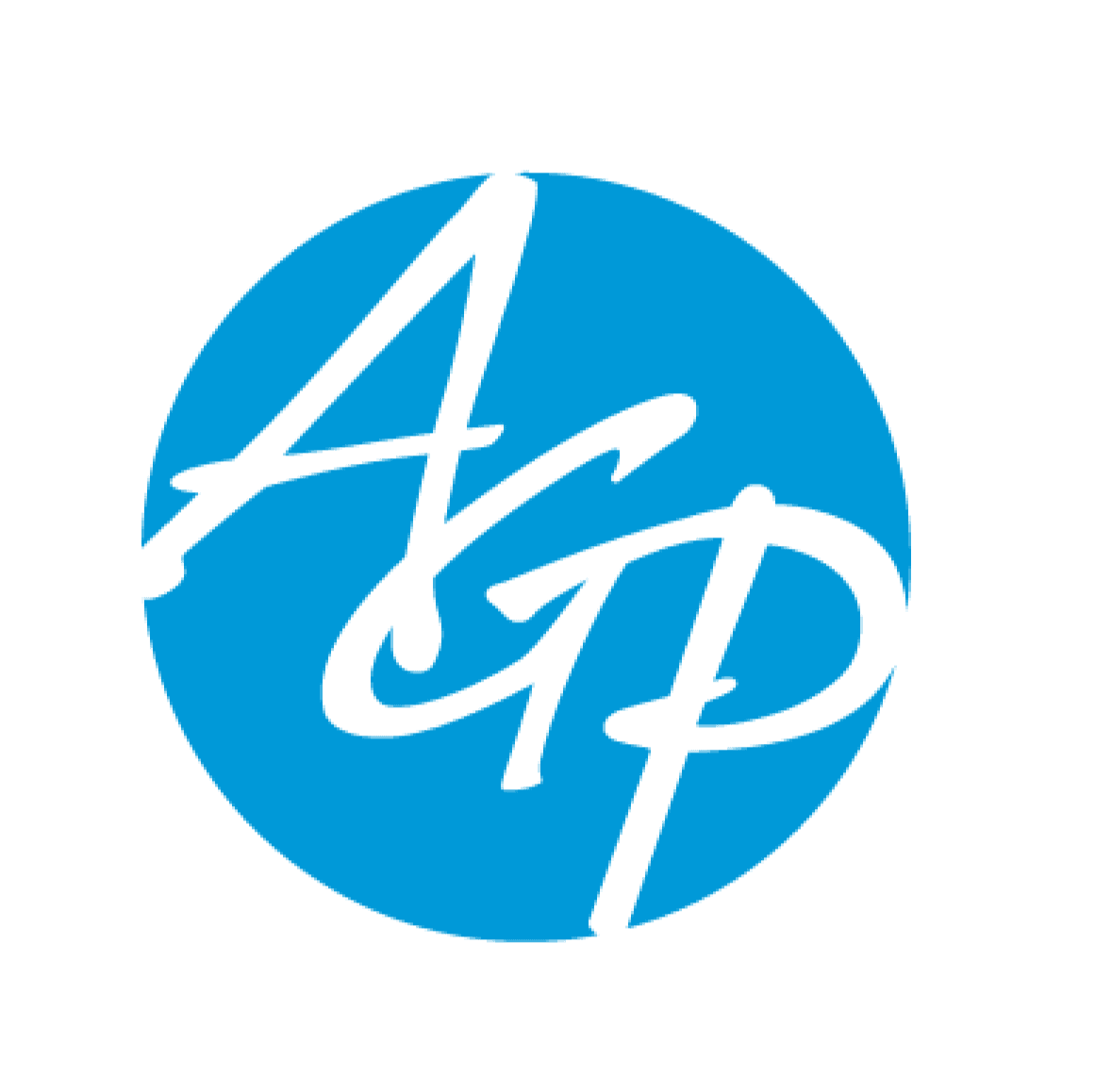
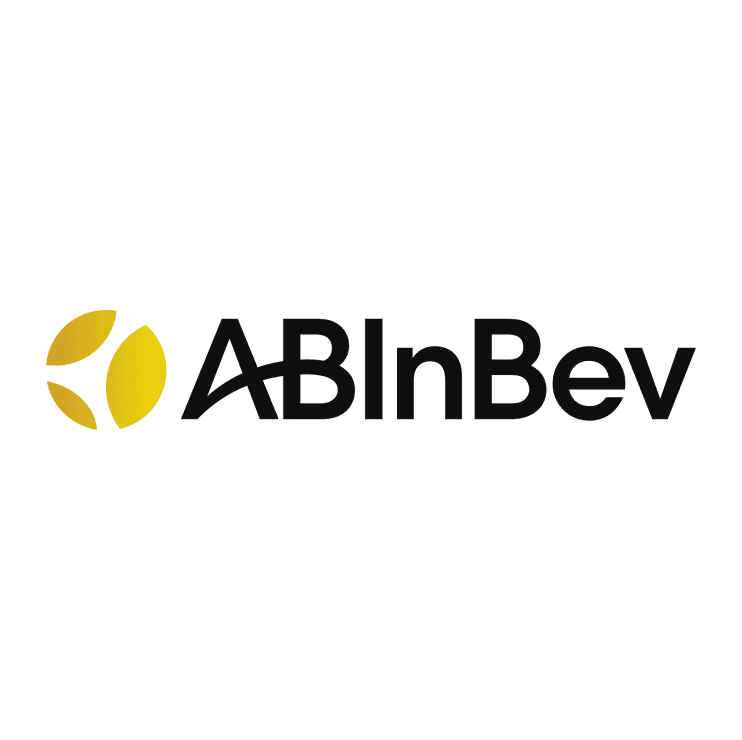
Summary
Ardagh Glass’s NextGen Furnace uses hybrid technology to reduce the carbon footprint of commercial-scale glass production, by replacing fossil fuel energy with renewable electricity.
Context
This case study is part of decarbonization best practices shared with AB InBev Eclipse sustainability program’s community. Discover more about the Eclipse program here.
Glass packaging is an energy-intensive industry
Glass packaging production is an energy-intensive industry that emits a significant amount of carbon dioxide from the combustion of natural gas in the furnace. The industry needs inventions and innovation to make it fit for a circular and climate-neutral economy - this can only be achieved by decarbonizing the glassmaking process.
New furnace design needed to deliver a step change
In 2020, Ardagh Group set its own challenging sustainability strategy targets, aligned with SBTi targets, to reduce carbon emissions from producing glass packaging, by 2030. Coupled with the EU pledge to be climate-neutral by 2050, it was clear that groundbreaking new furnace technology design, along with significant investment, was needed to deliver a step-change in the way glass container packaging is manufactured.
Reducing carbon emissions from the furnace by melting glass in a completely new way is a significant step towards achieving this goal.
Solution
A completely new furnace design
Designing the NextGen Furnace required Ardagh Glass Packaging (AGP) to completely rethink traditional furnace design, to allow it to switch from using predominantly natural gas, to using up to 80% electricity in the form of direct electrical heating, via electrodes powered by renewable electricity. The remaining energy is natural gas. In this way, carbon emissions are significantly reduced.
The first of its kind globally
Working with furnace supplier SORG, the hybrid furnace design is the first of its kind in the world. Based on an average of 60% electrical heating to date, it has successfully reduced carbon emissions in the production of glass packaging by 64% across Scope 1, 2 and 3 emissions per 330ml amber glass bottle produced in the furnace (ii) - AGP is striving to achieve more.
Saving 35,000 tons of carbon in the first year of production
In the first year of commercial production the NextGen Furnace has saved 35,000 tons of carbon. Depending on the production mix, this technology has the potential to save up to 45,000 tons of carbon every year (iii), compared to a conventional furnace.
Exceeding limits of other low-carbon technology
The new technology exceeds existing limits of all-electric glass furnaces - the only alternative low carbon technology currently available: it can produce glass containers on a commercial scale - up to 350 tons per day, compared to a maximum of 200 tons per day for all-electric melting; it can produce amber glass - the most challenging glass color to produce, plus other colors; it can use up to 70% recycled glass cullet to make new glass containers, unlike the limit of 50% for all-electric melting. This makes it a viable, low-carbon solution for the demands of the glassmaking industry.
Impact
Sustainability impact
Climate
This initiative targets Scope 1 and 2 emissions.
The hybrid-electric furnace achieved a 64% reduction in carbon emissions across Scopes 1, 2 and 3 based on an average electrical heating of 60% from January to June 2024. AGP's target is a reduction of up to 69% as it continues to gradually ramp up the electrical heating to a target of 80% (iv).
Scope 1 is impacted by switching melting energy from natural gas to renewable electricity, in addition to switching annealing energy from natural gas to renewable electricity.
Scope 2 is impacted solely from the switch to renewable electricity.
In its first year of operation, the hybrid-electric furnace has saved over 35,000 tons of CO2 in total.
Nature
This technology exceeds the limits of all electric melting in delivering a significant CO2 reduction compared to other currently existing technologies, whilst also maintaining a high level of recycled glass use (at 70%), thereby minimizing the use of virgin raw materials.
Social
This technology is contributing to a more stable future of the glass packaging industry and supporting job preservation across the complete value chain, by ensuring that glass packaging is a viable low-carbon packaging solution.
Business impact
Benefits
Operations: The hybrid-electric furnace breaks the limits of electrical melting so that commercial glass production can be done in a low-carbon way
Productivity: Productivity levels are maintained consistent with traditional technology. Output is at a commercial scale in the range of 280 to 320 tons per day
Employees: Jobs are secured thanks to consistent employment levels
Savings: The annual energy and heat savings achieved through the project are significant, but currently confidential
Costs
CAPEX Costs: The significant investment costs of this project were supported by an enabling grant from the German federal government.
OPEX Costs: Confidential information. However, costs are increased in line with the higher cost of using renewable electricity over natural gas.
Dependencies: The hybrid-electric furnace requires a reliable source of renewable electricity and sufficient local electrical grid capacity. AGP-Obernkirchen in Lower Saxony, Germany was selected as the location for the first hybrid-electric furnace because this facility meets these needs. The rollout of this technology will depend on the availability of the necessary electrical infrastructure. AGP, and the glass industry, are in discussion with relevant governments to press for these enabling conditions, in order to secure a low-carbon future for the industry.
Indicative abatement cost
Indicative abatement cost is not currently available for reasons of confidentiality.
Generally the abatement costs are comparable to a conventional melting furnace.
Impact beyond sustainability and business
Co-benefits
Scalable technology This technology is scalable to the wider glass industry (container glass and other sectors) and as such could be transformative at a global scale. The AGP team at Obernkirchen has hosted a number of visits for the wider glass community and its supply chain, as well as presenting at industry forums and key events. Subsequent hybrid melter applications in other sectors of the glass industry are under construction, with a glass tableware producer commissioning a Clean Melter in Portugal later in 2024.
Evolution of the project: using green hydrogen In the evolution of this project, AGP plans to switch the remaining natural gas to green hydrogen to fully decarbonize the melting energy used. A parallel project at AGP's Limmared facility in Sweden is currently running a hydrogen electrolyze, to ready the business for this next step.
Potential side-effects
No negative side-effects are envisaged from this project.
After twelve months in operation, AGP has experienced only positive side-effects:
Good quality commercial glass production
Learning how to use a completely new, low-carbon glass melting technology
The hybrid-electric furnace has been recognized with a number of prestigious awards both internationally and locally
The AGP-Obernkirchen site has hosted a number of high-profile visits from politicians and policy makers, resulting in significant media attention, such as from German Federal Minister for Economic Affairs and Climate Protection, in July 2024.
Implementation
Typical business profile
Companies operating with conventional glass furnaces for glass containers
Companies in other glass sectors
Transferable technology The hybrid-electric furnace is transferable to almost all currently existing conventional glass furnaces, as it is designed along the lines of conventional melting, which means it can adapt flexibly to other colors, cullet levels and daily tonnage. Within the European container glass industry, the estimated CO2 saving potential is significant, based on approximately 300 furnaces in Europe and 25 rebuilds per year. Other glass sectors (outside glass containers) can apply the technology too - a first tableware hybrid furnace will be operational in 2025.
Ideal conditions Geographically, the ideal location for hybrid-electric furnace technology has a strong electrical infrastructure, access to renewable electricity and sufficient grid capacity.
Phase 2 - Green Hydrogen Phase 2 of the hybrid-electric furnace will be to replace the remaining natural gas with green hydrogen. Any business considering this path will need access to hydrogen either from a hydrogen electrolyze or to be located within a hydrogen cluster.
Approach
The hybrid-electric furnace technology is available to all glass manufacturers through furnace supplier, SORG's Clean Melter.
A renewable electricity source is required to supply power to the furnace and the local electrical grid capacity must be sufficient to accommodate the increase in electricity used in the furnace.
Step-by-step implementation:
Initial operation: The hybrid-electric furnace began with 20% electrical heating and 80% oxy-gas combustion.
Electrical heating increase: Electrical heating has gradually risen to 60%, achieving stable commercial production and reducing CO2 emissions by 64%.
Current stage: Electrical heating will continue to increase towards 80%, potentially reducing CO2 emissions by up to 69%. Adjustments will be made in small steps to ensure stable commercial production.
Glass color production: Currently producing amber glass, with plans to test other colors (flint, green) based on commercial demand.
Next steps: Evaluation of potential amendments to the hybrid technology for new furnace installations within AGP.
Industry engagement: The NextGen hybrid technology has been presented at multiple glass technology conferences, and members of the global glass community have visited the furnace throughout 2024, with ongoing visits planned. This is intended to support the continued rollout of low carbon glass manufacturing across the sector.
Stakeholders involved
Internal Stakeholders involved
Project Leads within AGP:
Furnace Operations Group Manager
R&D Project Manager
Sustainability Director
Plant Director at AGP-Obernkirchen
Company functions: All business functions have worked together to support this project. E.g.
Operations (key to the planning, building and testing phases),
Procurement (tendered the contract to furnace suppliers),
Marketing (produced a video animation showing how the hybrid-electric furnace operates for customers, organized a three-day open event for customers, suppliers, media and MPs).
External Stakeholders involved
Main providers: SORG furnace supplier
Two major international beer brands have been among the first to benefit from having low-carbon bottles supplied from this ground-breaking furnace technology.
Key parameters to consider
Establishing the optimum level of electrical melting. This is an early stage innovation. The technology is completely new and involved rethinking existing furnace technology. It has been developed over several years, involving expertise from AGP, SORG and other key partners such as furnace refractory suppliers. The first build took nine months and is now in the ramp-up and validation phase. AGP and partner, SORG, aim to establish the optimum level of electrical melting to achieve the maximum carbon emissions reduction, while maintaining the quality of the glass produced.
Pre-requisites for this project: Access to a reliable renewable electricity source, and sufficient local electrical grid capacity, are pre-requisites for this project. As such, the geographical area selected for the project requires careful consideration.
Subsidies and electrical infrastructure: Subsidies may be available from local or national governments looking to support manufacturing industries to reduce carbon emissions and climate impact. AGP, along with other glass manufacturers and industry bodies, is actively lobbying European governments to provide the necessary electrical infrastructure that will enable the rollout of hybrid furnace technology.
Implementation and operations tips
The hybrid-electric furnace design is completely new, to allow the combination of up to 80% electrical melting (within the glass batch) and 20% oxy-gas combustion heating (over the glass batch). The furnace design has been developed by extensive computer modelling and technical discussion.
This is not a pilot furnace, it is a commercially operated, industrial-sized furnace.
Operating the furnace has required the development of new settings and procedures for a significant part of the operational window, as there is no reference available (other than computer modelling). This is an ongoing process throughout the phases of ramping up the electrical heating towards the target of 80%.
Source list
(i) 64% CO2 reduction based on average 60% electrical heating from Jan to June 2024.
(ii) Based on LCA calculation.
(iii) Saving up to 45,000 tonnes of CO2 per year, based on modelling.
(iv) A 2023 Life Cycle Analysis by Eunomia demonstrates the carbon savings per glass bottle to be produced in the NextGen Furnace, compared to a bottle from a conventional AGP furnace. A typical 330ml glass bottle produced in the conventional AGP furnace at Obernkirchen produces 140.1g of CO2, compared with one to be produced in the NextGen Furnace once fully operational at 80% renewable electricity and 20% gas, which is expected to produce 43g of CO2: a 69% reduction across Scope 1, 2 and 3 emissions.