Measure & Verify
- Introduction
- Step 1: Set boundaries
- Step 2: Collect & Calculate
- Get started: the GHG emissions calculation formula
- Identify and collect activity data for your GHG inventory
- Identify and collect relevant emissions factors
- Consolidate your company GHG footprint
- Digitize your inventory: streamline and automate GHG accounting
- Define and analyze metrics to prepare for decarbonization action
- Step 3: Verify
- Step 4: Improve and update
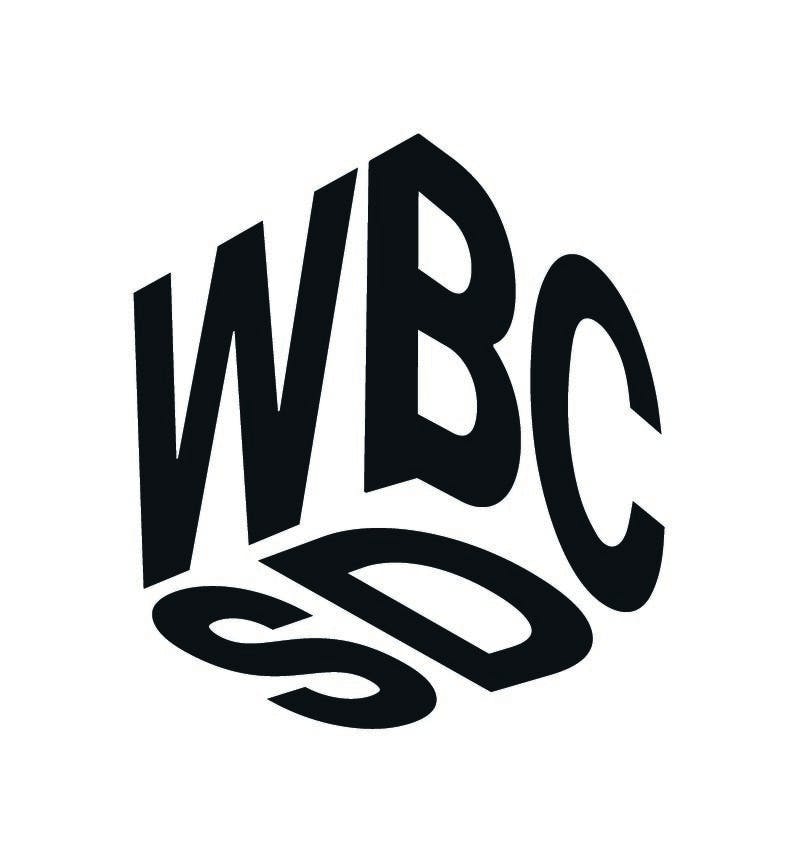
Consolidate your company GHG footprint
Two main approaches for consolidating your company GHG emissions
Your company GHG footprint aggregates the GHG emissions from activities and entities of your company following the organizational boundaries set earlier. This consolidation step is essential to build your overall company GHG footprint. Whether your company is centralizing data collection (i.e., performing calculation and aggregation centrally) or not (some may prefer to allow separate entities to calculate themselves before aggregating at company-level), it is essential that the organizational boundaries you selected are applied consistently to all levels of your organization.
There are two basic approaches for gathering data on GHG emissions at the corporate level: the centralized and decentralized approach. The difference between these two approaches is the level at which the emissions calculations occur (i.e., where activity data is multiplied by the appropriate emission factors) and in what type of quality management procedures must be put in place at each level of the corporation. Employees in facility functions are generally responsible for initial data collection without both approaches.
The two approaches are not mutually exclusive and should produce the same result:
1. Centralized
Individual facilities report activity data (such as quantity of fuel used) to the corporate level, where GHG emissions are calculated. This approach may be particularly suitable for office-based organizations.
Positives: Emissions calculations are standard across facilities.
Negatives: Creates distance between facility staff and the GHG emissions of their facilities and so may lead to lowered engagement (especially for following reduction strategies).
2. Decentralized
Individual facilities collect activity data, directly calculate their GHG emissions using approved methods and report this data to the corporate level.
This approach may be particularly suitable for organizations with complex facilities and significant process emissions.
Positives: Helps increase facilities' awareness on the topic of emissions
Negatives: May lead to resistance, increased training needs, an increase in calculation errors, and a greater need for auditing of calculations