Reduce
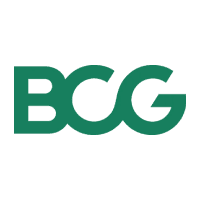
Apply abatement approaches in hard-to-abate sectors
Hard-to-abate sectors
Hard-to-abate sectors—titled as such because they face technological, economic, and possible policy barriers to decarbonization—pose a particular challenge for economy-wide Net Zero efforts. However, addressing these sectors is essential, as combined, the main hard-to-abate sectors make up 28% of all emissions (see Figure 2).

Figure 2: Emissions in hard-to-abate sectors. Sources: IEA; International Aluminum Org.; Transition Pathway Initiative; BCG Analysis.
With the main hard-to-abate sectors—Steel and Iron, Cement, Heavy Road, Chemicals, Shipping, Aviation, and Aluminum—contributing a significant share of global emissions, abatement strategies are necessary to reach Net Zero emissions. The need is urgent, as projections suggest that hard-to-abate sector emissions could grow by ~30% by 2050 if no action is taken (see Figure 3) (1). The IEA stated policies scenario is a conservative benchmark for future emissions that only takes into account existing and announced measures and policies, as opposed to pledges and objectives. Innovative, bold, and timely action is necessary to align these sectors with Net Zero.

Figure 3: Emissions in hard-to-abate sectors under the 2021 Stated Policies Scenario (Gt CO2). Sources: IEA; BCG Analysis.
Address the challenges of abatement
Emissions abatement is often difficult in these sectors for four interconnected reasons: supply economics, demand economics, technology, and policy.
Supply economics
An essential complication in many hard-to-abate sectors is the high abatement cost of implementing levers in those industries. Adjusting established production processes is often a capital-intensive endeavor requiring significant investment. Additionally, switching to green energy sources is typically expensive given technology barriers and the high energy intensity of these sectors. As these companies are typically commodity businesses operating in low profit-margin environments, any increase in cost due to a green premium (cost increase to produce sustainably) would be difficult to overcome.
Demand economics
A related complication in these sectors is that, while these changes require high capital investment, the return on investment is often unclear, as the demand for green products is nascent (e.g., green steel). While willingness to pay a green premium is beginning to emerge among buyers, it is not yet widely prevalent.
Technology
Existing technologies for decarbonization in these industries are often very limited, expensive, and some have not yet been proven at scale. In some industries, new processes and equipment may be needed to significantly decarbonize. Without sufficient market demand for these low-carbon approaches, technology development and deployment will be stymied.
Policy
Many of the goods produced (e.g., steel, aluminum) in these hard-to-abate sectors are manufactured and traded globally. Different countries and regions have adopted different approaches to decarbonizing these industries. In the US, the 2022 Inflation Reduction Act provides incentives for many hard-to-abate sectors (e.g., carbon capture, utilization and storage, clean hydrogen) (2). The EU has tended to implement decarbonization standards or targets, rather than provide incentives. Heterogeneous policy approaches in different regions add complexity to the global decarbonization of these industries.
Main decarbonization solutions for hard-to-abate industries
Despite challenges, technologies do exist to help companies in these sectors reduce their emissions. Viable abatement approaches in hard-to-abate industries vary and can often be quite particular. The abatement levers mentioned in the previous section are generally applicable to hard-to-abate industries as well, with (I) circularity/recycling, (II) material and process efficiency, and (III) renewable power often having low abatement costs in hard-to-abate industries with potential cost savings. However, for deep decarbonization these industries may need to rely on more expensive and bespoke levers in (V) new processes, (VII) fuel switch, including synthetic/biofuels and hydrogen fuel, and (VIII) carbon capture, use and storage. Costs are projected to come down in the coming years, especially with support from policies that support new technologies, such as subsidies for low-carbon hydrogen fuel in many regions, including the EU, India, the UK, the US, and Namibia (3).
Industry examples:
Cement
Major levers: Sustainable clinker use through alternative sourcing or reductions, energy efficiency, low-carbon fuels, material efficiency, and carbon capture.
Example: Holcim, a Swiss building material company, produced the first-ever 100% recycled clinker in their Altkirch, France plant in 2022. Clinker is the primary component in cement (and production of fresh clinker from limestone or similar materials is a significant source of carbon dioxide emissions), so this development will enable the company to create the first 100% recycled cement. The company plans to use this to make 100% recycled concrete in a facility made of 100% recycled materials (4).
Chemicals
Major levers: Vary by sub-industry; some examples across different sub-industries include material efficiency measures, optimized production processes, recycling, and reducing single-use plastics.
Ammonia example: In 2020, Trinidad Nitrogen Company, jointly owned by National Enterprises Limited and Yara, partnered with NewGen, a low-emission hydrogen energy project providing decarbonized hydrogen via water electrolysis as feedstock for its ammonia plant, reducing emissions from the production process. This partnership could have significant implications for global ammonia emissions, as Trinidad and Tobago is among the top ten ammonia producers globally (5). The project is expected to decrease carbon emissions by 165,000 tons annually (6).
Bioplastics example: Genomatica, a San Diego-based company, and Aquafil, an Italian sustainable textile company, successfully completed the first demonstration scale production runs for bio-based nylon-6 in 2022. This will create a material that is not just sustainably produced, but also sustainably disposed – a longtime barrier in creating sustainable plastics (7).
Aviation
Major levers: Low-carbon fuels, electric aircraft for short-hauls, aircraft and engine efficiency improvements.
Example: JetBlue and Shell Aviation began a partnership in 2023 to facilitate additional supplies of sustainable aviation fuel (SAF), bringing JetBlue’s use of sustainable fuels to 15% of its Los Angeles airport jet fuel uptake. The airline aims to convert 10% of its total fuel to SAF by 2030 (8). JetBlue is also investing in an airplane battery developer, Electric Power Systems (9). Electric aircraft may be suitable in the near term for low-capacity, short-haul flights.