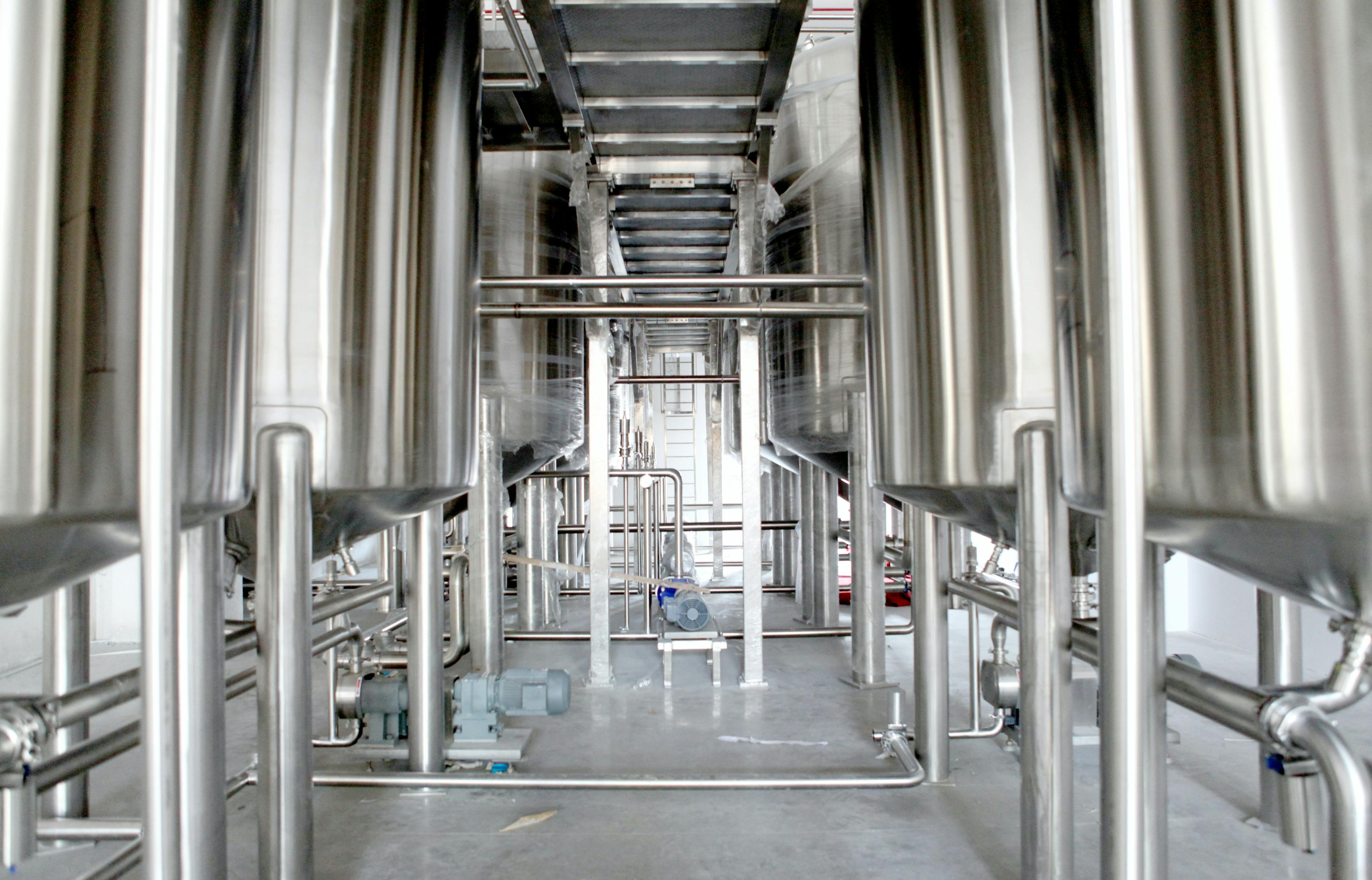
Invest in innovative pulping and paper making technologies
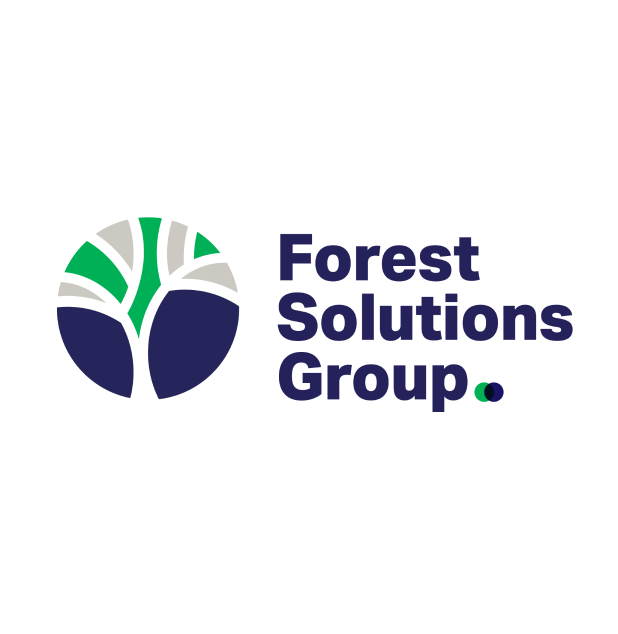
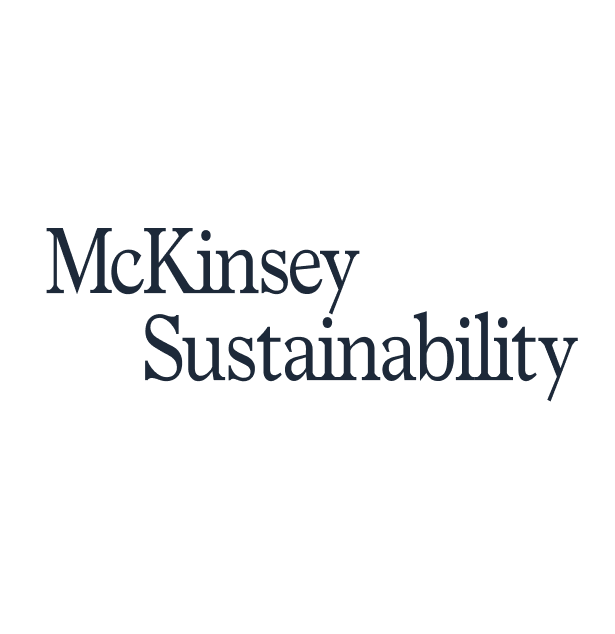
Summary
Adopting technologies that are more efficient than conventional methods will reduce GHG emissions from fuel combustion, and reduce the energy inputs associated with paper production
Key resources
Context
This Action is one of ten from the Catalogue of Key Decarbonization Actions, part of the Forest Sector Net-Zero Roadmap. Its objective is to support forest companies in the choice and implementation of actions to address emission hotspots and leverage the greatest opportunities for carbon removals.
LEVEL OF MATURITY | EMISSION ABATEMENT POTENTIAL | SHORT-TERM ECONOMIC FEASIBILITY | |
---|---|---|---|
LOW TO HIGH | LOW TO MEDIUM | LOW TO HIGH | |
• Level of maturity varies depending on the technology • TRL 3 – 9 | • Emission abatement ranging between 11 and 20% | • CAPEX: 5 – 20 million EUR depending on the configuration |
See methodology in the appendix section
Solution
The production of paper involves an energy intensive process, with paper drying consuming the most energy. Mills require low-, medium- as well as high-temperature heat from various sources, depending on the type of process (e.g., mechanical or chemical pulping, integrated and non-integrated mills), the equipment, as well as on the cost of the energy source (as mills will likely favour the cheapest and most readily available). In addition to enhancing heat recovery, it is vital to adopt technologies that are more efficient than conventional methods in order to reduce GHG emissions from fuel combustion, and can reduce the energy inputs required for each step.
Numerous technologies can help increase energy efficiency and decrease energy demand, particularly when combined with incremental process improvements, including the implementation of end-to-end process digitization and advanced analytics (e.g. advanced analytics set point optimization (1). Table 1 presents the top emerging technologies that were selected based on their abatement potential across all manufacturing stages, from pulping to paper drying. Additional levers that can increase energy efficiency in the mill through heat recovery are described in Action 3, Box 1: Other heat recovery technologies for pulping and paper making.
Table 1: Overview of the selected key technologies to increase energy efficiency in paper making (heat recovery technologies can be found under Action 3)
Process step | Technology | Description |
---|---|---|
Pulping | High efficiency refiner | A high efficiency refiner is a machine used in the papermaking process to refine the pulp and improve its properties. Installing a high efficiency refiner with new disks and design makes it possible to reduce the number of refiners in operation, and therefore energy consumption. |
High efficiency pulper | A high efficiency pulper combined with a new rotor design could provide more efficient pulping, reducing energy consumption. | |
Enzymatic treatments | Pre-formed enzymes are employed during the pulping process to pretreat lignocellulosic biomass before the production of pulp. | |
Forming | Turbo blower pump | A turbo blower pump is a high efficiency vacuum system technology. By replacing conventional liquid ring vacuum pumps, it allows for savings in energy consumption. |
Double dilution headbox | A double dilution headbox is a component used in papermaking machines to evenly distribute a diluted paper pulp slurry to form a uniform sheet of paper. The double dilution headbox uses two stages of dilution to achieve a more consistent and uniform distribution of fibers and reduces the flow passing through the screen and therefore the energy consumption. | |
Pressing | Shoe press | A shoe press is a type of paper press used to remove water from the paper web in the papermaking process. Installing a shoe press leads to improvements in dewatering: it increases the paper dry content before the dryer section and therefore the overall energy consumption required to dry the paper. |
Drying | Steel drying cylinders / Yankee | Steel drying cylinders enable improved heat transfer in the dryer cylinders due to a thinner shell. This makes the drying process more efficient and can achieve significant energy savings. |
Electromagnetic induction steel drying cylinder / Yankee | Using electromagnetic induction instead of steam energy to dry the paper reduces steam consumption in the drying paper process to zero. This allows for heat to be replaced by green energy. | |
Overall energy efficiency | Variable frequency drives | Instead of using a traditional “on/off” system, variable frequency drives optimize the energy consumed by motors by adjusting speeds to match load requirements. |
Online energy management system | These online systems use advanced analytics, real-time data monitoring and process control to analyse energy use and identify improvement opportunities, fine-tune and optimize the existing system energy use, and reduce the variability of energy consumption. They also enable to make decisions as to when to use green power generation instead of the grid. |
Source: McKinsey
Usage
Several of these technologies have already reached an advanced level of maturity in the industry, while some have recently emerged and are still at early stages of testing (see Table 2). Still, there are several pulp and paper mills where even mature technologies are not yet implemented or installed, which gives them the opportunity to reduce their CO2 emissions significantly (e.g. shoe presses only are installed in 55% of paper machines worldwide, despite their wide scale demonstration of efficiency). For some technologies such as the shoe press or steel drying cylinders, installation may require major rebuilds, including the building which houses the paper machine, that would need to be stopped for months, leading to revenue loss.
Table 2: Maturity level of the key selected technologies to increase energy efficiency in pulp and paper making
Section | Technology | Maturity (TRL) |
---|---|---|
Pulping | High efficiency refiner | Medium: 7-8. The solution is working in expected conditions or has gone through commercial demonstration. |
High efficiency pulper
| Medium: 7-8. The solution is working in expected conditions or has gone through commercial demonstration. | |
Enzymatic treatment
| Medium/high: 7-9. The solution is already commercially available, although some enzymatic treatment technologies are being tested and demonstrated. The technology requires further integration to ensure competitiveness. | |
Forming | Turbo blower pump | High: 9. The solution is commercially available, though it needs further improvement to be stay competitive. |
Double dilution headbox
| Medium: 5-6. Some prototypes have been proven at scale in conditions, but still need to be deployed. | |
Pressing | Shoe press | High: 9 (medium for tissue paper: 7-8). The solution is commercially available, although maturity is lower for tissue paper products. |
Drying | Steel drying cylinders / Yankee | High: 9. The solution is commercially available but needs further improvement to be stay competitive. |
Electromagnetic induction steel drying cylinder / Yankee
| Low: 3-4. Some early prototypes haven been proven to work in test conditions. | |
Overall energy efficiency | Variable frequency drives | High: 9. The solution is commercially available but needs further improvement to be stay competitive. |
Online energy management system
| Medium: 5-6. Some prototypes have been proven at scale in conditions, but still need to be deployed. |
Impact
Climate impacts
Targeted emissions sources
Adopting technologies for increased energy efficiency targets emissions due to fuel combustion as well as those due to use of electricity on site, steam, heating and cooling.
Emission abatement potential
The application of these technologies can achieve substantial energy efficiency gains and reduce GHG emissions. Adopting these technologies would lead to a 11-20% reduction in emissions (i). Given this range, each technology contributes to a different extent, as shown in Table 3.
Table 3: Emissions reduction potential of some technologies to increase energy efficiency in pulp and paper making
Section | Technology | Emissions reduction potential |
---|---|---|
Pulping | High efficiency refiner | Low |
High efficiency pulper | Low | |
Enzymatic treatment | Medium | |
Forming | Turbo blower pump | Medium |
Double dilution headbox | Low | |
Pressing | Shoe press | High |
Drying | Steel drying cylinders / Yankee | High |
Electromagnetic induction steel drying cylinder / Yankee | High | |
Overall energy efficiency | Variable frequency drives | Medium |
Online energy management system | High |
Business impacts
Benefits
Reduced costs through energy savings: Multiple technologies enable energy savings, which could lead to reduced operational costs.
Costs
Investment required: A typical project to reduce emissions, which includes the above-mentioned technologies, could cost about 5-20M EUR.
Operating costs: Some of these technologies are still emerging and others only available from 1-2 OEMs, who do not publicly disclose operating costs. Furthermore, the business case for implementing these technologies will be highly depending on current and future fuel mix and prices, therefore companies are recommended to do ‘their own due diligence’.
Indicative abatement cost: Abatement cost cannot be estimated due to the absence of operating costs estimates today.
Economic feasibility: The economic feasibility varies for each technology. Less mature technologies are likely to have low short-term economic feasibility despite their potential for significant emission reduction. The technology with the highest economic feasibility is typically used for forming, pressing and improving overall process energy efficiency.
Potential co-benefits and side effects
Co-benefits
Increased production speed: The adoption of some technologies like shoe press and steel cylinders makes it possible to increase paper production paper production speed. However, the opportunity to sell the additional volume will also depend on the market situation.
Side effects
Loss of revenues during installation time: For some technologies, the machines would need to be stopped for months during installation because of major rebuilds, which could create a revenue loss and other inconveniences during this time.
Implementation
These are the most common steps to adopt breakthrough technologies to increase energy efficiency in pulp and paper making:
Assess requirements: Forest companies should conduct a comprehensive energy assessment of the paper making process, which involves analyzing energy consumption patterns, identifying energy-intensive processes, and assessing opportunities for improvement through process optimization or the adoption of new technologies.
Select appropriate technology: Based on the comprehensive energy assessment, organizations should select technologies appropriate to the specific mill, considering factors such as cost, mill size and potential energy efficiency savings.
Install/upgrade equipment and processes: Replace outdated or energy-intensive equipment with more efficient alternatives. Install state-of-the-art technologies, such as high efficiency refiners and pulper, optimized drying technologies, and energy efficient motors and drives.
Key challenges/hurdles
Impact on final product quality and requirements: Energy efficient technologies can have a negative impact on the features and qualities of the product, which may disincentivize adoption.
Disruptions to production: Some technologies may require significant implementation time, creating costly disruptions to production.
Current limited premium on low carbon paper products: When consumers are willing to pay a premium for low-carbon products, this can serve as a significant incentive for producers to adopt energy-efficiency technologies. In the context of paper products, consumers’ willingness to pay a premium is limited today, and producers may not readily perceive the motivation for change.
First-mover challenges for low-maturity technologies: While most of the technologies have a medium to high maturity level (i.e. most have TRL above 7), a few are still in the earlier stages of development. In these instances, producers may encounter challenges associated with being early adopters, including issues like limited access to information, high capital investment, technological uncertainty, integration complexities with existing systems, limited vendor support, and difficulties in navigating the regulatory and policy landscape. In such a context, particularly smaller organizations may be reluctant to move forward in implementing new measures.
Potential solutions
Suitability assessment. Individual companies should assess each technology to ensure that product quality can be improved or maintained with the adoption of the technologies. Use of multi variant advanced analytics models will help fine tune recipes and process parameters to maintain product quality.
Plan installation/implementation to minimize production disruptions: Implementation of abatement measures can be planned to minimize operational disruptions, for instance by grouping the major rebuild items and planning minor interventions during scheduled maintenance or downtime.
Carry out cost due diligence and capture future premium. As demand for low-carbon paper products is expected to increase, McKinsey experts estimate that a 6-7% premium will emerge on low-carbon paper products.Furthermore, paper makers can carry out a cost due diligence on the above-mentioned decarbonization technologies. Most are already NPV positive today, and, depending on the region, regulation incentives, cost of energy, etc., technologies could be even more economically attractive.
Invest in R&D, and partner with research institutions and equipment suppliers to refine existing technologies and develop new breakthroughs. Further energy efficiency gains may require development of improved technology or better methods of applying technology to the current manufacturing process. Given the low maturity of some of the technologies, paper makers can engage with suppliers to co-invest into these initiatives.
Footnotes
(i) Note: McKinsey analysis.
Going further
Check out other Actions as part of the Forest Sector Net-Zero Roadmap:
Appendix
Methodology for assessment against criteria
Level of maturity: The level of maturity score for each action is based on the ‘Technology Readiness Level’ (TRL). This indicator estimates the maturity of technologies, measured through an assessment of their progress and capabilities. The scale originally ranges from 1 to 9, where TRL 1 is the lowest and TRL 9 is the highest. When a technology is at TRL 1, scientific research is underway and results are being translated into future research and development, while at TRL 9 the technology has already been proven to work. The International Energy Agency (IEA) has extended the TRL scale used in this report to incorporate two additional levels of readiness: one where the technology is commercial and competitive but needs further innovation efforts for the technology to be integrated into energy systems and value chains when deployed at scale (TRL 10). Finally, there is a level where the technology has achieved predictable growth (TRL 11).
Emission abatement potential: The emission abatement potential of each action, whether a technology or practice, describes the potential to reduce GHG emissions with respect to the counterfactual technology or practice, meaning the technology or practice that is part of the ‘business as usual’ scenario, or that is substituted or improved by adopting a decarbonization action. Emission abatement potential is usually expressed as a percentage, and the higher it is, the higher GHG emission reductions can be achieved:
Low = < 15% of GHG emissions Medium = 15-50% of GHG emissions High = > 50% of GHG emissions
Abatement cost: The abatement cost is an indicator that measures the costs associated with abating one ton of GHG emissions (EUR/ton CO2e abated). The lower the abatement cost, the cheaper it is to reduce emissions, and therefore the more attractive the action.
Short-term economic feasibility: Economic feasibility is assessed based on the maturity level and the abatement cost of each action, as per the visualization below. Actions with a low maturity level (≤ 4) are considered to have low economic feasibility in the short term, given the need to validate and deploy the technology in relevant environments. However, if the abatement cost has already proven to be low, the action is assessed as medium. Actions with medium maturity (TRL 5-8) may have low or medium economic feasibility in the short term, depending on the abatement cost (≤ 250 EUR/tCO2e). Similarly, the short-term economic feasibility of actions with higher maturity (TRL 9-11) varies depending on the abatement cost (low when < 550 EUR/tCO2e, medium if the cost ranges between 250-450 EUR/tCO2e, or high if the cost is lower than 250 EUR/tCO2e). The thresholds that determine short-term economic feasibility are defined by taking into consideration that additional benefit, including revenue generating opportunities. They are not monetized or included in the abatement cost estimates.