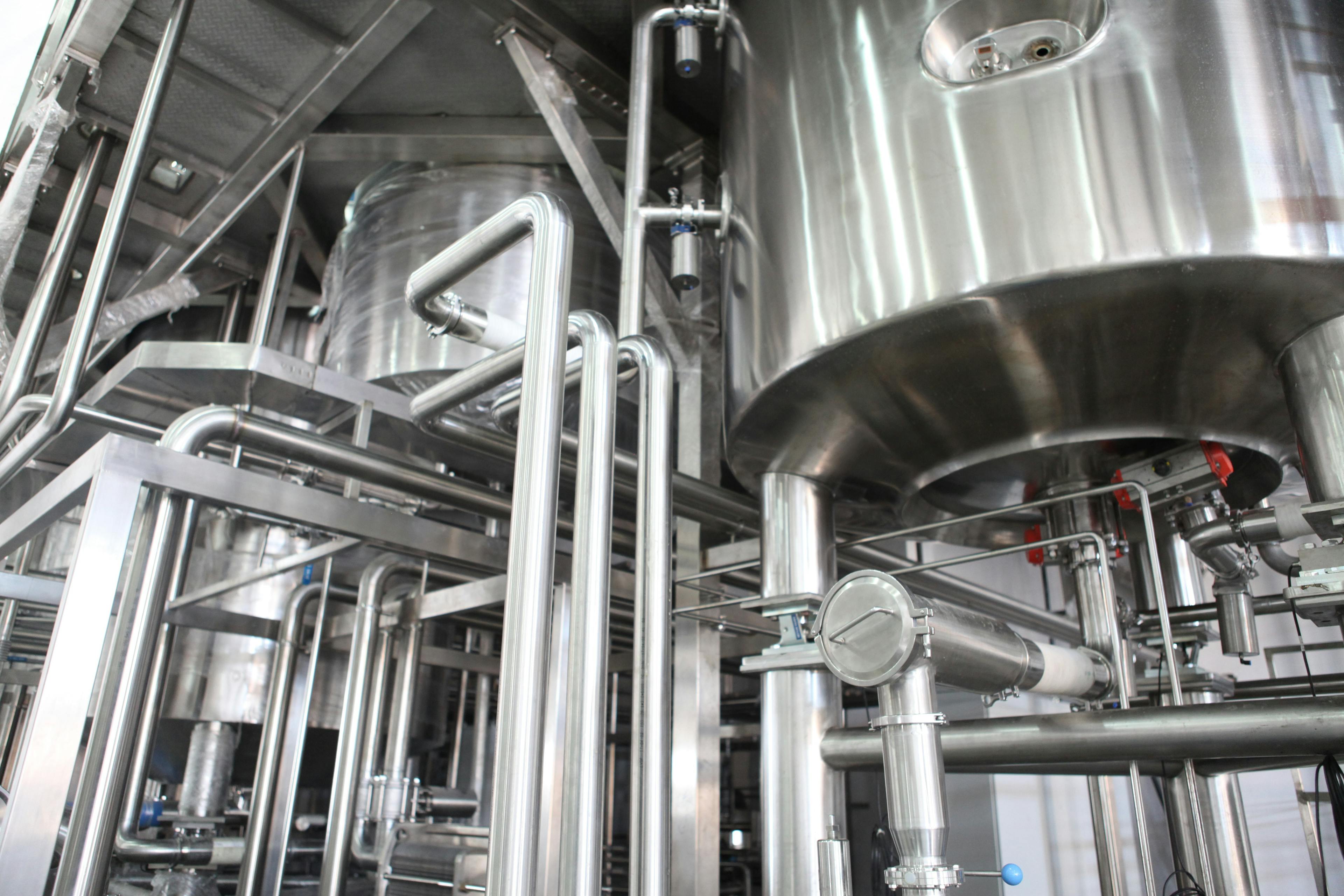
Switch to industrial electric boilers
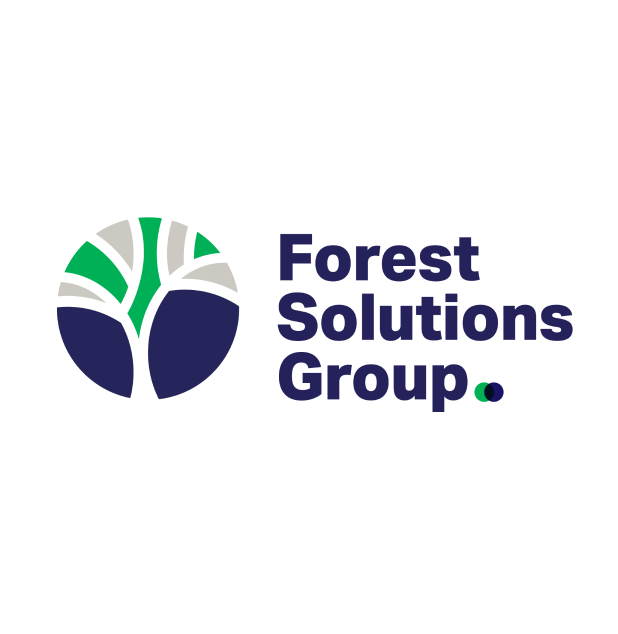
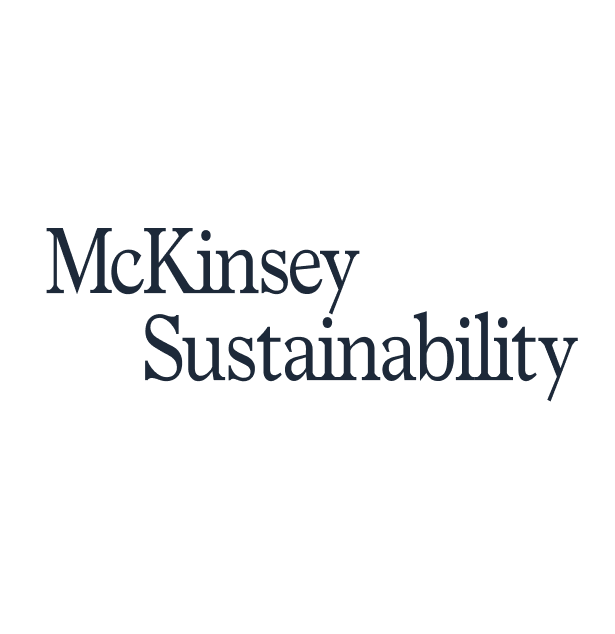
Summary
Electric boilers convert electricity into heat to produce steam, with almost 100% efficiency, reducing the greenhouse gas emissions typically associated with heat production
Key resources
Context
This Action is one of ten from the Catalogue of Key Decarbonization Actions, part of the Forest Sector Net-Zero Roadmap. Its objective is to support forest companies in the choice and implementation of actions to address emission hotspots and leverage the greatest opportunities for carbon removals.
LEVEL OF MATURITY | EMISSION ABATEMENT POTENTIAL | SHORT-TERM ECONOMIC FEASIBILITY | |
---|---|---|---|
HIGH | LOW TO HIGH | MEDIUM TO HIGH | |
• Commercially available • TRL 9-10 | • 100% abatement potential compared to fuel-powered boilers when using electricity from renewable sources • < 100% depending on grid carbon intensity | • CAPEX: 150 – 200 EUR/kW • Abatement cost: 130 – 450 EUR/tCO2 |
See methodology in the appendix section
Solution
Heat is used in the forest sector across industries (e.g. pulp and paper, textiles), and phases of the value chain (e.g. paper conversion and customization). Currently, most heat (in the form of steam) is produced in boilers, fuelled by either biomass or other fuels. When using fuels, particularly fossil fuels, heat production is associated with GHG emissions. To reach the highest abatement potential, electrification of heat must be combined with renewable electricity (procured or produced on site). If renewable electricity is not available, energy efficiency improvements associated with e-boilers can also indirectly reduce emissions.
Electric boilers convert electricity into heat to produce steam, with almost 100% efficiency, and only negligible energy losses. Commercially available electric boilers can provide low to high temperatures of up to 400°C, and steam with temperatures of up to 350°C and 70 bar. Therefore, electric boilers can meet the demands of both the pulp and paper industry, which usually requires heat at 200°C, and the textile industry, requiring up to 140°C (1). As Electric boilers can achieve high temperatures, their adoption can complement the adoption of, for instance, heat pumps (which are more energy efficient) to help achieve higher emission reductions for heat and steam production.
Electric boilers offer an added advantage as they complement existing installations and provide flexible generation. They can be easily switched on and off, and used during periods of excess energy when renewable sources produce more electricity due to favourable weather conditions (e.g. sunny and windy hours or days). As a result, operating electric boilers during low-cost electricity periods can lead to significant cost savings. Another benefit of electric boilers is their easy adoption, as they do not require retrofitting or conversion of infrastructure. They may however require large modifications to the steam and power, as well as to the boiler feedwater systems.
Box 1: Complementing electric boilers with long-duration thermal energy storage
Electric boilers can be complemented with long-term thermal energy storage technologies, which offer unprecedented benefits to store heat and sustain heat provision. Thermal storage technologies can store thermal energy for prolonged periods, providing system flexibility: by storing energy at times of surplus or when electricity prices are low, and releasing it when needed, long-term energy storage can help manage fluctuations in demand and supply and offers a way of integrating and providing flexibility to the entire energy system. This would in turn enable reduced costs for electricity. Thermal storage technologies are already available and can be scaled at low marginal costs (2).
Figure 1: An electrode boiler for steam and hot water (3)

Electrode boilers are a type of electric boiler that use electricity flowing through streams of water to create saturated steam. They automatically adjust the water level in the boiler to heat only what is required. When there is no demand, they deactivate. The boiler in the figure has up to 75 MW capacity in one unit.
Usage
Electric boilers are commercially available, and the technology can be easily adopted (TRL 9-10), as installation is straightforward and does not require a complete redesign of primary processes (i). As electric boilers provide a low emission and high efficiency way of producing heat and steam, they can be adopted by all relevant industries. This includes the forest sector, as processes such as pulping, paper making and textile manufacturing require steam. Although the adoption of electric boilers is not yet widespread, there are several examples of companies switching to electric boilers to reduce their carbon footprint.
The most common barrier to the increased adoption of this technology is the high costs compared to fuel-fired boilers. Although electric boilers require a similar capital investment as the conventional alternatives (for medium- and high-temperature heat applications), the financial benefit of electrification depends on the difference between the ongoing costs of energy to run electric equipment and conventional fuel equipment.
Currently, average electricity prices are usually higher compared to conventional fuels in most locations, which makes electric boilers more costly compared to e.g. natural gas boilers. However, some actions, such as price arbitrage (i.e. the process of buying and selling electricity in different markets at different prices in order to exploit the differences in electricity prices between different locations, time of day, or seasons) or storing electricity (e.g. through Thermal Energy Storage) can help make it a positive business case already today.
An additional obstacle to higher adoption is the availability of the electricity grid infrastructure. Electric boilers increase the electricity demand considerably, and the adoption of electric boilers must be supported by the grid.
Impact
Climate impacts
Targeted emissions sources
The adoption of electric boilers replaces emissions from fuel combustion in traditional boilers, although emission abatement potential is entirely dependent on the energy sources.
Emission abatement potential
When electricity is purchased from the grid, emission reduction will depend on the local energy mix.
When renewable electricity is purchased (e.g. with Power Purchase Agreements) or generated on-site, electric boilers can achieve 100% operational emissions reduction compared to fuel-powered boilers. The generation of a CO2-free electricity grid would lead to complete decarbonization of the processes requiring heat and steam.
Business impact
Benefits
Reduced carbon costs: Reduced carbon costs in countries where a carbon price is applied to industrial emissions, in the form of a carbon tax or an emissions trading scheme. Small facilities may already be exempt.
Increased supply security: Supply security can be increased by reducing the reliance on (often) imported fuels, although this also requires additional investments in grid reliability.
Simple operations: Electric boilers can also offer several benefits in terms of operations: electric boilers do not require any fuel handling system, and are safer as there is no risk of gas leaks, other hazardous emissions or combustion-related hazards. Maintenance is often reduced, thanks to the compact design and less maintenance requirements. They offer precise temperature control to match heat needs.
Costs
Investment required: Initial investment for industrial electric boilers ranges between 150–200 EUR/kW, including Installation costs. However, contextual variables can introduce supplementary charges. For instance, additional costs may arise if upgrades to the distribution systems, grid connections, boiler feedwater system or steam condenser are required. In this instance, initial investment can be as high as 400-500 EUR/kW (ii).
Operating costs
Operating costs typically depend on local electricity prices. Current electricity prices are variable and may range between 25 and 60 EUR per MWh, although it’s important to keep in mind that strategies to reduce reliance on the grid and achieve lower costs exist, such as price arbitrage and thermal energy storage. Additionally, there are other operating costs, such as grid charges, costs for the internal power distribution system and for the water feed system, as well as fixed costs (e.g. insurance premiums, annual inspections, permits, safety equipment, training, maintenance, and administrative costs).
Indicative abatement cost
The abatement cost depends on the cost of electricity and on the emission-intensity of electricity in the location: it can range from 130 EUR/tCO2eup to 450 EUR/tCO2e (iii).
Potential co-benefits and side effects
Co-benefits
Improved safety and reduced regulatory requirements: Electric boilers are a safer boiler design, as they do not pose risk of gas leaks or risk of burnings or explosions when there are fuel lines, flumes, flames or storage tanks.
Side effects
Risk of increased emissions in the short term: If a company exclusively uses electricity from renewable sources (generated on-site or purchased via agreements), it can completely eliminate operational GHG emissions from heat and steam generation. However, if the company relies on electricity from the grid, the GHG emissions associated with using an electric boiler will vary depending on the local energy source mix. In countries with limited energy generation from renewable sources, the electrification of steam boilers can potentially increase annual GHG emissions, due to higher GHG emission factors of the electricity grid compared to other fuels, which cannot be offset by the higher efficiencies of electric boilers. For example, in many countries around the world, using natural gas to power a boiler results in a lower carbon footprint than using electricity.
Implementation
These are the most common steps to switch to electric boilers in manufacturing:
Assess requirements: Determine the specific heating needs of the organization, such as the required heating capacity, operating pressure, and temperature.
Select the appropriate equipment: Select an electric boiler that suits the heating requirements of the paper mill. Consider factors such as boiler capacity, efficiency, reliability, and compatibility with the existing system.
Adapt existing infrastructure: Ensure that the electrical infrastructure is installed to support electric boilers and that the boiler water feed systems meets quality requirements. This may involve upgrading the electrical system, installing additional wiring, connecting to the grid and providing the necessary electrical connections to power the boilers if generation is on-site.
Install and commission the boilers: Install the electric boiler. Once the electric boilers are installed, they need to be commissioned. This involves performing initial start-up procedures, testing the boilers for proper operation and verifying their performance according to the design specifications. Optimize use, balancing heat requirements and operating patterns based on renewable electricity price and availability.
Key challenges/hurdles
Higher operating costs: Besides the fact that electricity prices are typically higher than the prices of conventional fuels such as natural gas, electrification may also involve additional costs such fees for grid connection.
Potential solutions
Identify cost savings: Operating electric boilers during low-cost electricity periods can reduce the cost of operation. Additionally, a cost benefit analysis may determine that higher operating costs can be offset by energy use reductions and avoided carbon costs associated with the use of electric boilers.
Footnotes
(i) Note: Rademaker K., Marsidi M. (2019). Decarbonisation options for the Dutch paper and board industry. PBL Netherlands Environmental Assessment Agency & ECN part of TNO, The Hague
(ii) Note: Based on FSG members’ assessment
(iii) Note: McKinsey analysis
Going further
Check out other Actions as part of the Forest Sector Net-Zero Roadmap:
Appendix
Methodology for assessment against criteria
Level of maturity: The level of maturity score for each action is based on the ‘Technology Readiness Level’ (TRL). This indicator estimates the maturity of technologies, measured through an assessment of their progress and capabilities. The scale originally ranges from 1 to 9, where TRL 1 is the lowest and TRL 9 is the highest. When a technology is at TRL 1, scientific research is underway and results are being translated into future research and development, while at TRL 9 the technology has already been proven to work. The International Energy Agency (IEA) has extended the TRL scale used in this report to incorporate two additional levels of readiness: one where the technology is commercial and competitive but needs further innovation efforts for the technology to be integrated into energy systems and value chains when deployed at scale (TRL 10). Finally, there is a level where the technology has achieved predictable growth (TRL 11).
Emission abatement potential: The emission abatement potential of each action, whether a technology or practice, describes the potential to reduce GHG emissions with respect to the counterfactual technology or practice, meaning the technology or practice that is part of the ‘business as usual’ scenario, or that is substituted or improved by adopting a decarbonization action. Emission abatement potential is usually expressed as a percentage, and the higher it is, the higher GHG emission reductions can be achieved:
Low = < 15% of GHG emissions Medium = 15-50% of GHG emissions High = > 50% of GHG emissions
Abatement cost: The abatement cost is an indicator that measures the costs associated with abating one ton of GHG emissions (EUR/ton CO2e abated). The lower the abatement cost, the cheaper it is to reduce emissions, and therefore the more attractive the action.
Short-term economic feasibility: Economic feasibility is assessed based on the maturity level and the abatement cost of each action, as per the visualization below. Actions with a low maturity level (≤ 4) are considered to have low economic feasibility in the short term, given the need to validate and deploy the technology in relevant environments. However, if the abatement cost has already proven to be low, the action is assessed as medium. Actions with medium maturity (TRL 5-8) may have low or medium economic feasibility in the short term, depending on the abatement cost (≤ 250 EUR/tCO2e). Similarly, the short-term economic feasibility of actions with higher maturity (TRL 9-11) varies depending on the abatement cost (low when < 550 EUR/tCO2e, medium if the cost ranges between 250-450 EUR/tCO2e, or high if the cost is lower than 250 EUR/tCO2e). The thresholds that determine short-term economic feasibility are defined by taking into consideration that additional benefit, including revenue generating opportunities. They are not monetized or included in the abatement cost estimates.