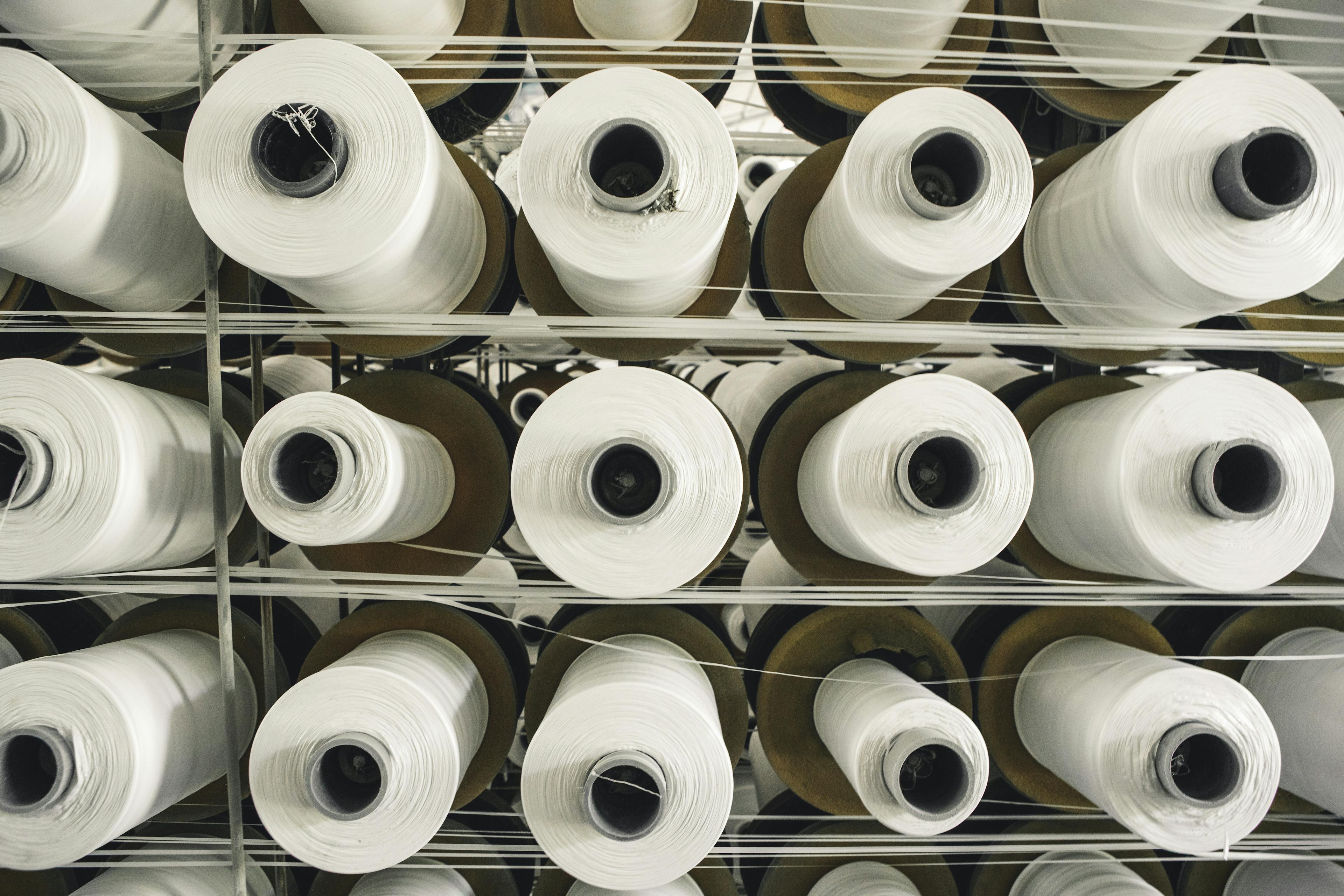
Adopt heat recovery technologies in the pulp mill
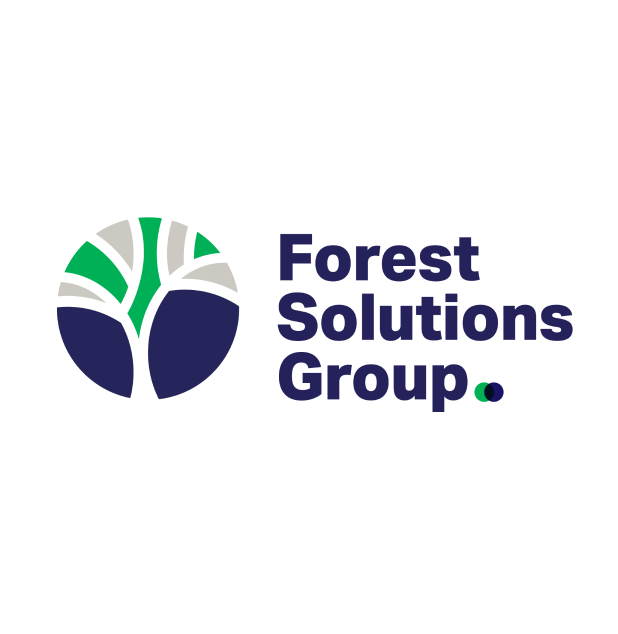
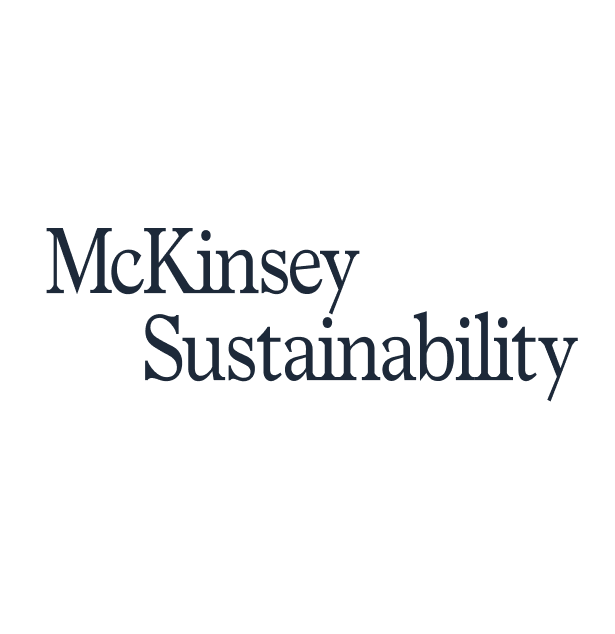
Summary
Adopting heat recovery technologies in the pulpmill can increase efficiency of operations, recovering waste generated as a by-product of the pulping and papermaking process.
Key resources
Context
This Action is one of ten from the Catalogue of Key Decarbonization Actions, part of the Forest Sector Net-Zero Roadmap. Its objective is to support forest companies in the choice and implementation of actions to address emission hotspots and leverage the greatest opportunities for carbon removals.
LEVEL OF MATURITY | EMISSION ABATEMENT POTENTIAL | SHORT-TERM ECONOMIC FEASIBILITY | |
---|---|---|---|
LOW TO HIGH | MEDIUM TO HIGH | MEDIUM TO HIGH | |
• Level of maturity varies per technology and temperature range of heat pump • TRL 4 - 11 | • 20% - 80% Compared to natural gas boiler and depending on local electricity mix | • CAPEX: 200 – 1200 EUR/kW • Abatement cost: 0 – 100 EUR/tCO2 |
*See methodology in the appendix section
Solution
Heat recovery technologies are vital to increasing the energy efficiency of mill operations, as they can recover waste heat generated as a by-product of the pulping and papermaking process. Most of this heat cannot be reused otherwise, as it has a high level of humidity and/or contains unwanted gaseous or particulate contamination.
Among all heat recovery technologies applicable in the pulp and paper mill (see Box 1), mechanical heat pumps offer the greatest potential for heat recovery and energy efficiency for existing facilities. These devices transfer and upgrade thermal energy from waste heat sources to ‘heat sinks’ using a small amount of additional energy – usually from electricity. More detail on heat pumps functioning can be found in Figure 1. In contrast to an absorption heat pump, mechanical heat pumps are driven by electrical (rather than thermal) energy.
Industrial heat pumps are substantially more efficient at heating than conventional boilers: the coefficient of performance (COP) can be as high as 300-400% in heat pumps achieving low-temperature lifts while conventional heating systems usually offer an energy efficiency level (1). When performing heat lifts, the difference between the input and output temperatures can be between 30‐50°C for heat pumps currently on the market (2). Analysis from CEPI found that the application of heat pumps to paper drying can achieve potential energy savings of more than 50%. Nevertheless, while mechanical heat pumps constitute an important decarbonization action for existing old facilities, more efficient heat recovery technologies are available and should be prioritized over mechanical heat pumps in the case of new facilities.
Figure 1: Simple diagram of a mechanical heat pump (3)

The graph above visualizes the processes of a mechanical heat pump, where an operating fluid circulates inside a closed circuit. A heat source, which can be industrial waste heat or environmental heat, transfers heat at low pressure and low temperature. The heated operating fluid is compressed by an electrically driven compressor, which also raises the temperature. The heat can be transferred and used at higher temperatures. Following heat extraction, the operating fluid is depressurized in the expansion valve, which causes a further decrease in temperature. Heat pumps, as well as other heat recovery technologies, can be applied to multiple phases of the pulping and paper making process. Paper drying in particular offers a high potential for heat recovery. Paper drying is energy intensive, as it requires heat and steam at high temperatures. Heat pumps can be integrated in the process to further optimize heat recovery, as shown in Figure 2.
Figure 2: Integrating heat pumps in paper making (4)

Following heat transfers to pre-heat the incoming air feeding the drying sections of a paper machine, the latent heat of the water vapour recuperates via the drying hood, and could be used to evaporate the refrigerant in the heat pump. The refrigerant is compressed and returns to liquid form, while the resulting heat is used to evaporate the condensate coming from the drying cylinders. To lift the steam to higher pressures, steam compressors are installed. Fresh steam from boilers can be added to ensure pressure control in the cylinders (5).
Box 1: Further heat recovery technologies for pulping and paper making
Heat recovery technologies can be applied to multiple phases of the pulping and paper making process, and through different technologies, including and not limited to:
Heat exchangers: These devices are used to heat or cool a process fluid to a desired temperature, and can also improve a system’s energy efficiency by transferring heat between two or more process streams. Studies found a 15% reduction in energy adopting heat recovery technologies in multi-cylinder dryers using heat exchangers (6).
Absorption chillers: These devices use waste from other processes or equipment to produce and distribute chilled water for cooling needs. They are different from other chillers in that they do not have a compressor. Instead, they dissolve the vapor in an absorbent. The resulting product is transferred to a higher-pressure environment using a pump with low electricity demands. It can be used for gas turbine inlet air-cooling applications, outdoor applications in hazardous areas and bleaching.
Organic Rankine Cycle: These systems can convert low-grade waste heat into electricity with efficiency levels ranging from 5% to 15%. These systems consist of components like generators, condensers, and evaporators, and they come in diverse sizes. Additionally, ORC systems are adaptable for recovering medium-grade heat from sources like recovery boilers, requiring heat in the range of 90-150 degrees Celsius
Stationary siphons and mechanical vapor decompensations: These devices can replace the dryers in the paper machine, and help achieve 5-10% efficiency gains.
Closed hood for paper machines: Closed hoods for paper machines, instead of an open or semi-open system, are specially designed drying and ventilation systems used to save steam and heat, reducing energy consumption and associated GHG emissions.
Usage
As it stands, heat pump adoption in the forest sector, including in pulp and paper and the textile industry, is limited in comparison to other sectors such as the food and tobacco industry, machinery, transport equipment and chemicals (Figure 3). However, there has been some increase in uptake due to the benefits of improved energy efficiency (7)
Figure 3: Adoption of heat pumps in different industries (8)

Adoption is largely inhibited by the high cost of electricity compared to marginal fuel cost and the limited commercial availability of high-temperature heat pumps, achieving temperatures above 90°C (see Table 1). In fact, there are only a few pioneering manufacturers demonstrating temperatures in the range of 120–165°C, and a number of research projects are developing heat pumps that aim to demonstrate sink temperatures in the range of 160– 200°C (9).
Table 1: Industrial heat pump technology readiness by temperature range (10)
Temperature range | Technology readiness level (TRL, 1-11) | Example of process in the pulp and paper industry |
---|---|---|
<80 °C | TRL 11: Proof of market stability | De-inking |
80-100 °C | TRL 10: Commercial and competitive, but large-scale deployment not yet achieved | Bleaching |
100-140 °C | TRL 8-9: First-of-a-kind commercial application in relevant environments | Paper drying |
140-160 °C | TRL 6-7: Pre commercial demonstration | Pulp boiling |
160-200 °C | TRL 4-5: Early to large prototype | Steam production |
> 200 °C | TRL 4: Early prototype | High temperature steam production |
Impact
Climate impact
Targeted emissions sources
Heat pumps can substantially reduce emissions by improving energy efficiency, displacing fuels, reducing heat waste, and by using electricity sourced from an increasingly low carbon grid.
Emission abatement potential
Emission reductions will depend on the energy efficiency gains and on the emission intensity of the local electricity grid. According to IEA, emission reduction compared to a gas boiler can range between 20% to 80% in countries with cleaner electricity. In the EU, heat pumps can currently achieve approximately 50% emission reductions compared to a natural gas boiler. However, current estimates do not account for future decarbonization of the grid, which would result in even higher emission reductions. Moreover, off-grid solutions (e.g. when electricity is generated on-site through renewable sources) could reduce emissions even further.
Business impact
Benefits
Potential operational cost reduction: Depending on the prices for natural gas and electricity, heat pumps may lead to reduced costs per unit of heat.
Reduced costs by reducing the need for emission allowances: Applicable to countries where emissions trading schemes exist and apply to the industry (11).
Increased supply security:
When using local renewable sources, improved supply security can be achieved by reducing the reliance on (often) imported fuels (12)
Costs
Investment required: Capital cost of industrial heat pumps currently ranges between 200-1,200 EUR/kW, depending on temperature range, capacity and other factors.
Operating costs: Due to the limited utilization of high temperature industrial heat pumps, comprehensive data on their operational costs remains scarce. Existing studies suggest a range of approximately 20 – 50 EUR/MWh (13) (i). Yet any estimate is expected to evolve as technology advances, adoption increases and the market for renewable energy develops. In fact, operating costs depend on both electricity prices (and consequentlyon future supply, demand, the geographical location and local subsidies) and the coefficient of performance. Heat pumps can help achieve substantial cost savings, ranging between 30-80% compared to other systems (e.g. an electric boiler only). Heat pumps with higher COP and lower temperature lifts can achieve the higher savings, while those achieving higher temperature lifts (and therefore with lower COP) are closer to the lower bound.
Indicative abatement cost:
Abatement costs depend on the price of electricity and gas in each country, as well as on the set-up, industry size and processes. Estimates range between slightly negative abatement cost (14) to just above 100 EUR/tO2e (15).
Potential co-benefits and side effects
Co-benefits
Air quality in the factory
Heat pumps reduce fuel combustion on-site, leading to improved air quality in the factory and in the surrounding areas. This can in turn deliver health benefits to workers and the local population (16)
Side-effects
As illustrated in Figure 4, industrial heat pumps are large devices, which weigh up to two tonnes and may require large installation rooms (up to 70 m2, although smaller models exist). Therefore, the installation of heat pumps requires substantial changes to the process. Companies can consider adding them during the refurbishment of existing facilities, allowing for the additional time required.
Figure 4: Model of a high temperature heat pump (Source: Siemens)

The image shows an illustrative heat pump, with a capacity of 9-70 MW and heat sink up to 160 C°. Heat pumps can weigh several tons, and take up several m2: the smallest heat pumps (e.g. 0.1 MW) may take up less than 2 m2, while those with larger capacities may require up to 70 m2 for installation.
Implementation
These are the most common steps to adopt heat recovery technologies in the pulp mill:
Energy savings potential requirements: As explained in the implementation section of Action 2, an energy audit will help to understand the mill’s energy consumption patterns, identify areas for heat absorption, and quantify the potential savings. Analysis of the current heating systems, including boilers, kilns and dryers can determine heat requirements and opportunities for heat recovery.
Select the appropriate equipment: Select an appropriate heat pump system that suits the specific requirements of the pulp mill. Consider factors such as the desired output, temperature requirements, efficiency, and reliability. Companies may benefit from consulting with heat pump suppliers and experts to determine the most suitable system.
Adapt existing infrastructure: Modify the pulp mill’s infrastructure to accommodate the heat absorption system, undertaking necessary changes to piping, ductwork and electrical connections.
Install and commission the heat-pump: Install the heat absorption system. Ensure correct integration with existing heating systems and follow best practices for installation, including insulation, sealing, and safety measures. Once the installation is complete, conduct thorough commissioning and testing of the heat pump system. Make any necessary adjustments, based on initial tests, in order to ensure optimal performance.
Key challenges/hurdles | |
• Availability of suitable heat pumps: commercially available heat pumps typically are not designed to handle the temperatures required in some phases of the pulp and paper manufacturing process, including paper drying and pulp boiling (17). | |
• Physical constraints: industrial absorption heat pumps may not be suitable for some pulp mills, especially for small producers, due to their size or require substantial redesign of the production process. | |
• Shortage of qualified installers (18): key heating markets are experiencing undersupply of qualified installers, which may deter companies from installing heat pumps due to concerns about quality and delays to installation. | |
Potential solutions | |
• Combine steam heat pump with a steam compressor: this can help to mitigate the problem of commercial heat pumps not yet able to achieve very high temperatures, as the compressor compresses the steam directly, recovering the heat and using low-grade waste heat to generate high-temperature steam. | |
• Engage with suppliers and invest in R&D: manufacturers of pulp and paper could partner with heat pump manufacturers to develop specialised heat pumps capable of handling the temperatures used in production and to increase compatibility with existing infrastructure and processes (e.g. reducing size). | |
• Collaborate with government, training providers and heat pump manufacturers: organizations can work with relevant stakeholders to increase the supply of heat pump installers. Measures can include advocating for the creation of financial incentives for workers to train in the industry, providing work placement opportunities and ensuring the integration of expertise in industrial applications as part of training programs. |
Footnotes
(i) Note: Agora Industry, FutureCamp (2022): Power-2-Heat: Gas savings and emissions reduction in industry
Going further
Check out other Actions as part of the Forest Sector Net-Zero Roadmap:
Appendix
Methodology for assessment against criteria
Level of maturity: The level of maturity score for each action is based on the ‘Technology Readiness Level’ (TRL). This indicator estimates the maturity of technologies, measured through an assessment of their progress and capabilities. The scale originally ranges from 1 to 9, where TRL 1 is the lowest and TRL 9 is the highest. When a technology is at TRL 1, scientific research is underway and results are being translated into future research and development, while at TRL 9 the technology has already been proven to work. The International Energy Agency (IEA) has extended the TRL scale used in this report to incorporate two additional levels of readiness: one where the technology is commercial and competitive but needs further innovation efforts for the technology to be integrated into energy systems and value chains when deployed at scale (TRL 10). Finally, there is a level where the technology has achieved predictable growth (TRL 11).
Emission abatement potential: The emission abatement potential of each action, whether a technology or practice, describes the potential to reduce GHG emissions with respect to the counterfactual technology or practice, meaning the technology or practice that is part of the ‘business as usual’ scenario, or that is substituted or improved by adopting a decarbonization action. Emission abatement potential is usually expressed as a percentage, and the higher it is, the higher GHG emission reductions can be achieved:
Low = < 15% of GHG emissions Medium = 15-50% of GHG emissions High = > 50% of GHG emissions
Abatement cost: The abatement cost is an indicator that measures the costs associated with abating one ton of GHG emissions (EUR/ton CO2e abated). The lower the abatement cost, the cheaper it is to reduce emissions, and therefore the more attractive the action.
Short-term economic feasibility: Economic feasibility is assessed based on the maturity level and the abatement cost of each action, as per the visualization below. Actions with a low maturity level (≤ 4) are considered to have low economic feasibility in the short term, given the need to validate and deploy the technology in relevant environments. However, if the abatement cost has already proven to be low, the action is assessed as medium. Actions with medium maturity (TRL 5-8) may have low or medium economic feasibility in the short term, depending on the abatement cost (≤ 250 EUR/tCO2e). Similarly, the short-term economic feasibility of actions with higher maturity (TRL 9-11) varies depending on the abatement cost (low when < 550 EUR/tCO2e, medium if the cost ranges between 250-450 EUR/tCO2e, or high if the cost is lower than 250 EUR/tCO2e). The thresholds that determine short-term economic feasibility are defined by taking into consideration that additional benefit, including revenue generating opportunities. They are not monetized or included in the abatement cost estimates.