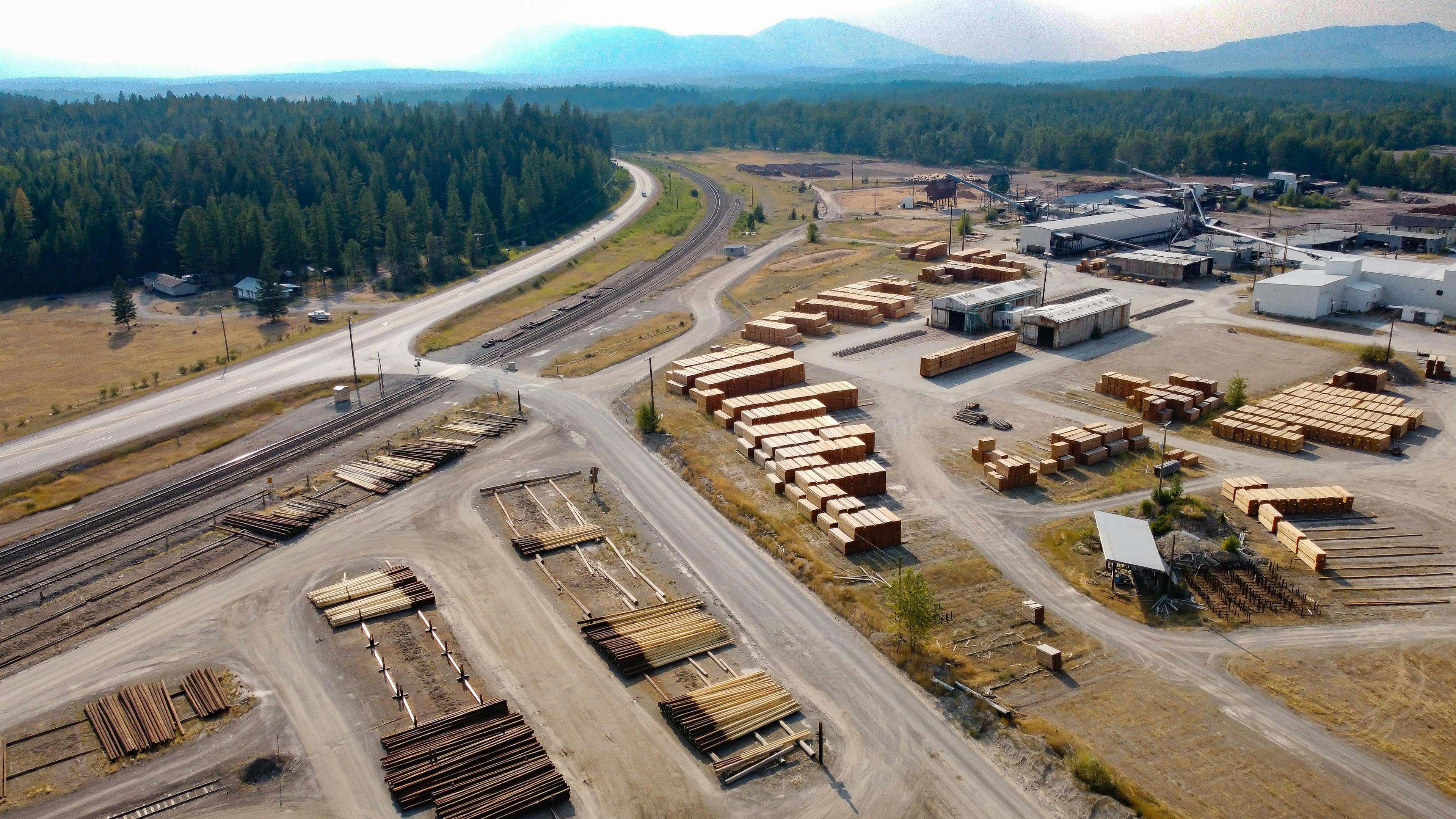
Adopt heat recovery technologies in the sawmill
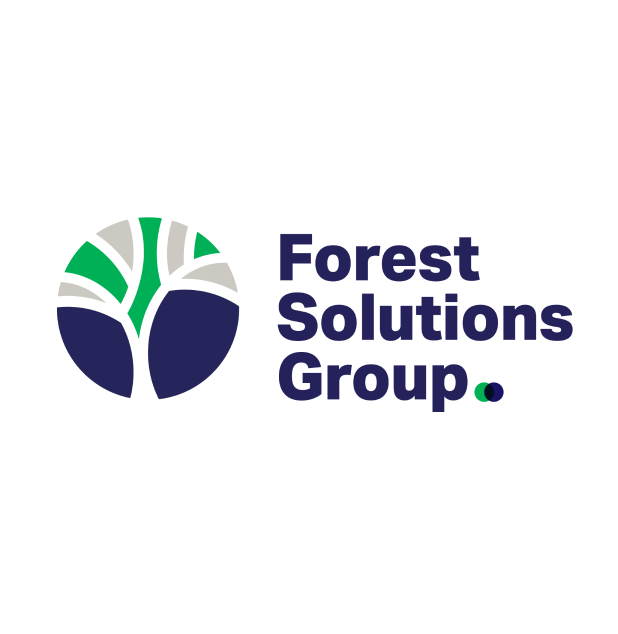
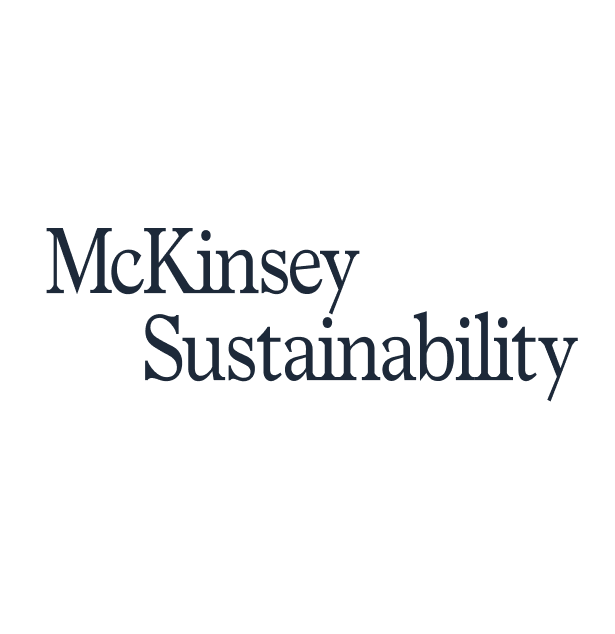
Summary
Adopting heat recovery technologies in the sawmill can increase efficiency and reduce heat loss which saves energy, reduces fuel combustion and emissions associated with operations.
Key resources
Context
This Action is one of ten from the Catalogue of Key Decarbonization Actions, part of the Forest Sector Net-Zero Roadmap. Its objective is to support forest companies in the choice and implementation of actions to address emission hotspots and leverage the greatest opportunities for carbon removals.
LEVEL OF MATURITY | EMISSION ABATEMENT POTENTIAL | SHORT-TERM ECONOMIC FEASIBILITY | |
---|---|---|---|
MEDIUM TO HIGH | LOW TO HIGH | LOW TO HIGH | |
• First-of-a-kind commercial demonstration to operation in relevant environment • TRL 8 – 9 | • 0 – 70% compared to the counterfactual and on the energy source | • CAPEX: 400 – 2000 EUR/kW • Abatement cost: 200 – 800 EUR/tCO2 depending on size, capacity and technology |
See methodology in the appendix section
Solution
In the sawmill, fuel is used to operate machinery such as debarkers and saws, and power drying kilns that dry wood (logs or chips). Wood drying is often the most energy-intensive phase, requiring high heat demand and conventional drying systems unequipped with heat recovery technologies that may ‘waste’ up to 80% heat through losses (1). To address this inefficiency, heat recovery technologies, such as heat exchangers or heat pumps, can be employed to increase efficiency and reduce heat loss in the sawmill, particularly in the drying kilns. By adopting these technologies, the sawmill can save a significant amount of energy, leading to reduced fuel combustion and GHG emissions associated with the sawmill operations.
Figure 1: Heat demand (MJ) per kg of evaporated water for different heat recovery technologies (2)

Among other heat recovery technologies (see Box 1), absorption heat pumps are best placed to increase energy efficiency in sawmills but are still in the early stage of development and are the most CAPEX intensive of the heat pump options (3). Absorption systems (or alternatively absorption heat pumps) are devices that can efficiently increase the temperature of waste heat given from a heating source, therefore reducing the heat required (see Box 1). Differently from heat pumps, the absorption systems use an additional ‘absorber’, which dries the saturated air from the kiln and recirculates either air or water into the drying kiln or the generator. Moreover, whereas a mechanical heat pump is driven by electric energy, an absorption heat pump is driven by thermal energy. For this reason, they are more suitable to sawmills where energy can be produced through biomass combustion, and overall require the least heat supply (see Figure 1 for a comparison of several heat recovery technologies in the sawmill). Key features of absorption systems are that they can deliver a far higher temperature lift (the temperature difference between waste heat temperature and upgraded process heat temperature) than the other systems. Their energy performance does not decline steeply at higher temperature lift, and they can be customized for combined heating and cooling applications. In theoretical studies, absorption heat pumps were found to reduce heat demand by up to 70% (4).
The graph compares the performance of four different systems: one conventional system with no heat recovery technologies, and three more with distinct heat recovery technologies, including absorption systems. The graph shows the amount of energy required to evaporate one kg of water from the dried wood. Absorption systems have the best performance. Mechanical heat pumps have higher energy efficiency (reducing heat demand by 100%) but require higher electricity inputs (in vivid green). Absorption heat pumps reduce energy demand by ~70% but require no additional electricity (5). Note: the heating period is identical across technologies, and it is the amount of energy needed to start the drying process.
Figure 2: Illustrative example of a heat pump used in the chemical industry (6)

Box 1: Other heat recovery technologies in the sawmill
Other heat recovery technologies applicable in sawmills are (7):
Heat exchangers: These devicesuse the thermal energy in the air leaving the kiln to heat the cold air entering the kiln, thereby increasing energy efficiency. Heat exchangers are the most used recovery technology for the industrial kiln dryer, continuous drying kilns as well as in belt driers for wood chips or bark. Heat exchangers are well known, have low operation costs after installation, and can achieve substantial energy efficiency gains: belt driers equipped with heat exchangers can deliver up to 35%-55% energy efficiency gains (i).
Dehumidification kilns with mechanical heat pumps: The air exiting the drying kiln, with a high moisture content, is circulated to an evaporator, where water condenses. This cools the air, and the condensed water flows down a drain. Parallelly, an electricity or steam-powered compressor increases the pressure of the heat pump’s working fluid. The high-pressure refrigerant gas goes from the compressor to the condenser, where the gas condenses, in turn releasing heat. The cool dry air absorbs the heat from the fluid, and then warm dry air is recirculated in the system. While dehumidification kilns with mechanical heat pumps are an effective technology for heat recovery in the sawmill, they use a substantial amount of electricity to power the compressor.
Usage
Although heat recovery technologies, including absorption systems, have been around and commercially available for many years (TRL 8-9), their adoption in sawmills is not yet widespread according to the available literature. There is evidence of heat pumps being adopted into newly built drying kilns, especially in northern European countries, but their overall application may still be limited in most parts of the world. Adoption could be limited by the relatively high capital costs, especially for smaller sawmills (8). Moreover, lack of awareness about heat recovery technologies among sawmill operators, technical challenges (e.g. in installation, process re-design, etc.) or even geographical factors (e.g. efficiency in cold climates) can all represent potential barriers to more widespread adoption among smaller sawmills.
Impact
Climate impact
Targeted emissions sources
Absorption systems help reduce GHG emissions from fuel combustion in sawmills by increasing energy efficiency.
Emission abatement potential
The potential for reducing emissions through heat recovery technologies is closely tied to their ability to improve energy efficiency, as well as the energy sources utilized in the sawmill. For instance, open absorption systems can reduce heat demand by nearly 70%. However, in cases where sawmills rely heavily on biomass, the emissions abatement potential may be negligible, while it can reach up to 70% when fossil fuels are utilized.
Business impact
Benefits
Reduced costs for biomass and opportunities for revenues: Increased energy efficiency can help reduce consumption of biomass for energy, allowing the production of biofuels for external use. Adopting heat recovery can therefore deliver benefits that go beyond emissions reduction by minimizing energy costs and potentially providing additional revenues through the sale of saved biomass. Cost reductions may also be achieved through relevant industry emissions trading schemes.
Reduced costs by reducing the need for emission allowances: Applicable to countries with relevant industry emissions trading schemes.
Optimise operations: Absorption heat pumps, as well as other heat recovery technologies, can also help sawmills optimize operations, as heat recovery systems can be controlled to adapt to external conditions. For instance, heat recovery systems can be operated when outside temperatures are high and heating energy demand is low and vice versa, by saving heating power in winter when temperatures are low. This results in a substantial reduction in the heating power needed for the dryer and in improved management of the process over winter, when cold temperatures and freezing periods can create delays due to insufficient heat production.
Costs
Investment required: Depending on the technology installed, upfront investment varies: absorption heat pumps may cost from 400-2000 EUR/KW.
Operating costs: The operating costs for absorption heat pumps depend on the source of energy used. Assuming sawmills would use mostly woody biomass from bark, chips and lower-quality logs, the operating price may range between approximately 10 and 90 EUR/MWh (considering the price of woody biomass from 10-80 EUR/MWh, and the maintenance costs 2-10 EUR/MWh) (ii) (9). The availability of biomass on-site as well as the (current and future) prices for biomass have a large role in determining (iii).
Indicative abatement cost: Abatement costs depend intrinsically on the prices operating costs, therefore on the current and future prices of biomass in each country, as well as on the set-up, the industry size and the processes. Estimates range between 20-160 EUR per tonne of CO2e (10) (iv).
Potential co-benefits and side effects
Co-benefits
Air quality in the factory: Unlike fuel-powered heating, absorption systems and electric heat pumps produce heat without producing onsite emissions, improving air quality in the factory and surrounding areas. This can in turn deliver health benefits to workers and the local population (11).
Side-effects
Impact on process: As illustrated in Figure 2 industrial absorption heat pumps take up a lot of space and the installation may require substantial changes to the sawmills’ set-up and processes.
Implementation
These are the most common steps to adopt heat recovery technologies in the sawmill:
Assess energy savings potential and requirements: Conducting an energy audit will enable the company to determine its heat requirements and identify prospects for heat recovery. The audit will identify areas where energy is being wasted due to inefficient equipment, outdated technology or operational practices that can be improved, quantify the potential savings and recommend energy conservation measures. Furthermore, the audit may yield additional insights related to the lifetime of the energy systems and equipment, the relative GHG emission intensity of local electricity sources, and the availability of local, state, or federal incentives to facilitate financing. Moreover, audits may underscore potential gaps in local employee knowledge in the domains of energy efficiency and emissions reduction.
Select the appropriate equipment: Select an appropriate heat pump system that suits the specific requirements of the sawmill. Consider factors such as the desired output, temperature requirements, efficiency, and reliability. Companies may benefit from consulting with heat pump suppliers and experts to determine the most suitable system.
Adapt existing infrastructure: Modify the sawmill's infrastructure to accommodate the heat absorption system, undertaking necessary changes to piping, ductwork and electrical connections.
Install and commission the heat recovery technology Conduct the installation of the best-suited heat recovery technology. Ensure proper integration with existing heating systems and follow best practices for installation, including proper insulation, sealing, and safety measures. Once the installation is complete, conduct thorough commissioning and testing of the heat pump system. Make any necessary adjustments, based on initial tests, to ensure optimal performance.
Key challenges/hurdles
Physical constraints: industrial absorption heat pumps may not be suitable for some sawmills, especially for small producers, due to their size or require substantial redesign of the production process.
Shortage of qualified installers (12): key heating markets are experiencing undersupply of qualified installers, which may deter companies from installing heat pumps due to concerns about quality and delays to installation.
Potential solutions
Engage with suppliers and invest in R&D: Manufacturers of pulp and paper could partner with manufacturers to advance research and development on heat pumps, so to increase compatibility with existing infrastructure and processes (e.g. by reducing size).
Collaborate with government, training providers and heat pump manufacturers: Organizations can work with relevant stakeholders to increase the supply of heat pump installers. Measures can include advocating for the creation of financial incentives for workers to train in the industry, providing work placement opportunities, and ensuring the integration of expertise in industrial applications as part of training programs.
Footnotes
(i) Note: Stela (2021). A third less energy required – Stela belt dryer with heat recovery for HS Timber Group
(ii) Note: Agora Industry, FutureCamp (2022): Power-2-Heat: Gas savings and emissions reduction in industry
(iii) Note: Agora Industry, FutureCamp (2022): Power-2-Heat: Gas savings and emissions reduction in industry
(iv) Note: McKinsey analysis
Going further
Check out other Actions as part of the Forest Sector Net-Zero Roadmap:
Appendix
Methodology for assessment against criteria
Level of maturity: The level of maturity score for each action is based on the ‘Technology Readiness Level’ (TRL). This indicator estimates the maturity of technologies, measured through an assessment of their progress and capabilities. The scale originally ranges from 1 to 9, where TRL 1 is the lowest and TRL 9 is the highest. When a technology is at TRL 1, scientific research is underway and results are being translated into future research and development, while at TRL 9 the technology has already been proven to work. The International Energy Agency (IEA) has extended the TRL scale used in this report to incorporate two additional levels of readiness: one where the technology is commercial and competitive but needs further innovation efforts for the technology to be integrated into energy systems and value chains when deployed at scale (TRL 10). Finally, there is a level where the technology has achieved predictable growth (TRL 11).
Emission abatement potential: The emission abatement potential of each action, whether a technology or practice, describes the potential to reduce GHG emissions with respect to the counterfactual technology or practice, meaning the technology or practice that is part of the ‘business as usual’ scenario, or that is substituted or improved by adopting a decarbonization action. Emission abatement potential is usually expressed as a percentage, and the higher it is, the higher GHG emission reductions can be achieved:
Low = < 15% of GHG emissions Medium = 15-50% of GHG emissions High = > 50% of GHG emissions
Abatement cost: The abatement cost is an indicator that measures the costs associated with abating one ton of GHG emissions (EUR/ton CO2e abated). The lower the abatement cost, the cheaper it is to reduce emissions, and therefore the more attractive the action.
Short-term economic feasibility: Economic feasibility is assessed based on the maturity level and the abatement cost of each action, as per the visualization below. Actions with a low maturity level (≤ 4) are considered to have low economic feasibility in the short term, given the need to validate and deploy the technology in relevant environments. However, if the abatement cost has already proven to be low, the action is assessed as medium. Actions with medium maturity (TRL 5-8) may have low or medium economic feasibility in the short term, depending on the abatement cost (≤ 250 EUR/tCO2e). Similarly, the short-term economic feasibility of actions with higher maturity (TRL 9-11) varies depending on the abatement cost (low when < 550 EUR/tCO2e, medium if the cost ranges between 250-450 EUR/tCO2e, or high if the cost is lower than 250 EUR/tCO2e). The thresholds that determine short-term economic feasibility are defined by taking into consideration that additional benefit, including revenue generating opportunities. They are not monetized or included in the abatement cost estimates.